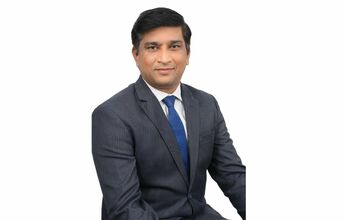
Keerthi Prakash, Managing Director, Renault Nissan Automotive India Pvt Ltd
Keerthi, with changing consumer preferences, including a focus on sustainability and electric vehicles, what steps is RNAIPL taking to align its products and strategies with these trends?
In February 2023, the Renault-Nissan Alliance announced an investment worth Rs 5,300 crore in India to design and manufacture six new models - three each for Renault and Nissan, including an electric vehicle for each brand -first in India. These models will be manufactured by RNAIPL and will be targeted at both domestic and export markets. This decision, made after a deep evaluation of market conditions and customer preferences reflects the Renault Nissan Alliance's commitment to India for the years to come.
Furthermore, RNAIPL remains dedicated to embracing advanced manufacturing techniques that optimise production processes, reduce waste, and enhance overall efficiency. This aligns with our commitment to pursuing innovation in other spheres besides technology. We are also deeply committed to sustainable and smart manufacturing practices and are working towards achieving carbon-neutral operations by 2045.
Looking ahead, how do you anticipate the automotive industry to evolve, and what role do you see RNAIPL playing in shaping this evolution?
The automotive industry, both in India and globally is being shaped by several factors. The most important of these factors is perhaps the rapid evolution of customer preferences. Additionally, technological advancements are allowing us to build better quality and safer vehicles in line with environmental considerations. These are just some of the factors that will shape the success of automotive players.
RNAIPL was established in 2008 and we recently celebrated our 15th anniversary since foundation. We produced the first car in May 2010 and since then we have successfully manufactured more than 2.5 million cars for Nissan and Renault for India's domestic market as well as exports. More than 1.15 million cars manufactured at our Chennai plant have been exported to over 108 destinations globally in line with our ‘Make in India, Make for the World' philosophy and our production milestones have allowed us to establish ourselves as a centre of excellence for manufacturing cars.
We are moving ahead to an exciting future, bringing the latest and best global technologies from Nissan and Renault to customers in India and other markets. We are currently gearing up preparation activities at our plant to produce six new vehicles that are designed keeping in mind the demands of the Indian customers. The preparation activities include technology and skill upgradation as well as knowledge sharing with the other Nissan and Renault plants around the world.
Take EV for example, although it will be the first time that we will manufacture EVs at RNAIPL, there is a wealth of know-how within Nissan and the Alliance about the production of EVs. Recently Nissan crossed the 1 million milestone for sales of EVs and as you would know Nissan Leaf which was first launched in 2010 has sold more than 6,50,000 units globally in over 50 markets. So, what we're working through is the transfer of this know-how. And this is done through training. We've got teams from RNAIPL visiting the Nissan plants in the UK and Japan to become master trainers. We are also consulting with other plants in our network and other stakeholders in preparation for the launch.
The company is known for its state-of-the-art manufacturing facilities. What are the key factors that contribute to maintaining manufacturing excellence and high-quality standards? How does the company leverage technology and innovation to streamline production processes and ensure efficient operations?
RNAIPL has a rich manufacturing heritage, where we combine the best standards from two global automotive manufacturers- Renault and Nissan. We follow a production standard called ‘The Alliance Production Way' which brings together the best practices from both entities, focusing on synergies and innovation. Our manufacturing excellence and highquality standards have evolved around developing the right processes with the right infrastructure and the right skill sets. We aim to build it right and build it right the first time.
Any new process development takes place during the product development stage as it evolves from the concept stage to trials and mass production. Our extensive know-how and heritage along with our emphasis on innovation allows us to determine the right level of infrastructure required. In terms of skillsets, RNAIPL has an elaborate and extensive management process for tracking skills from basic to advanced managed on a zone-wise basis.
Basic skill training is provided through the Regional Training Centre where the operators' skill for quality and time is validated through structured training. Advanced skills are imparted through Master trainer and train-the-trainer programmes including deployment to other Alliance plants. We have several internal indicators to track plant performance and productivity including equipment efficiency, defects, quality as well as digitalisation. The latter is a key priority for us, and we aim to improve efficiency and make RNAIPL a better place to work with a better focus on what customers need from us. We have a clear digital strategy to work towards these goals and are building a digital architecture that will be scalable for our future needs.
Sustainability is increasingly crucial in the automotive sector. How you are integrating sustainable practices and technologies into its operations and vehicle offerings?
Sustainability is a core pillar of our operations at RNAIPL, and we are working to reduce the impact of our operations on the environment. Our goal is that by 2045, our operations at RNAIPL will be carbon neutral. We are working to reach this goal with a three-pillared strategy which currently helps us save nearly 87,500 tons of CO2 emissions every year. The pillars are Reducing the energy consumption of our operations; Increasing our use of renewable energy; and Implementing energy-efficient technologies.
On energy sources, currently, almost 60 per cent of the electricity consumed at our plant is generated from renewable sources such as solar and wind. We are working to expand our in-house solar plant capacity from 2.2 MW at present to 14 MW by 2026 through additional rooftop solar panels and floating solar panels in the plant's pond. With that infrastructure in place, we will be able to fulfil 85 per cent of our energy needs through renewable power by 2030, and eventually 100 per cent by 2045.