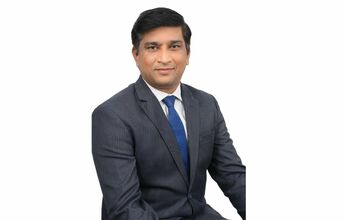
Keerthi let's talk about your journey and experience in the automotive industry that led you to the role of Managing Director at Renault Nissan Automotive India…
I have been very fortunate in my nearly three decades of professional experience to have worked in a variety of roles that allowed me to get a 360-degree understanding of the automotive industry. I started my professional journey as a junior engineer with TAFE (Tractors and Farm Equipment Ltd) following my education in Mechanical Engineering. After about three years, I had the opportunity to work with Toyota, working initially in the body shop, I then moved on to other aspects of manufacturing including production engineering, logistics, lean production, and kaizen.
In 2008, I joined Renault Nissan Automotive India Pvt. Ltd., just when it was being set up. Over the last 15 years, I have had the chance to take up several senior roles within RNAIPL and Nissan covering vehicle production, plant engineering, industrial strategy new product development industrial strategy, both in India and overseas- specifically in Japan and in the UK. I took up the role of Deputy Managing Director of RNAIPL in February 2021 leading on Engineering, Quality Assurance, Production Control & Parts Arrangement. In August 2022, I stepped up to the role of Managing Director of the plant.
Interesting and quite inspiring journey it is! However, what core values and leadership principles do you believe have contributed to your success in leading a prominent automotive company?
I believe that adopting a ‘people first' or ‘humancentric' approach is essential to success in any organisation, not just for manufacturing or automotive. After all, people are the most important resource of any organisation. Additionally, we spend most of our waking lives at work and hence our workplace becomes an important part of our lives, and it is therefore essential to make the workplace a fulfilling experience for all employees. At RNAIPL, our processes are designed to keep the well-being of the employees, for example, ergonomics is an important consideration during the design stage of any new process. Secondly, we also try to bring a bit of home to the workplace by creating rest areas where employees can have photographs of their family members or important life events displayed.
Having an open mind, that is having the curiosity to learn and accept new challenges is always key to personal and professional development. We believe in five core principles that should guide all our actions. These are respecting others and society, always thinking of the customer, showing facts and facing reality, being accountable and acting proactively and finally also thinking out of the box as we believe that innovation is the key to delivering the best products at great value to our customers. Innovation is one key driver that helps us to constantly evolve and stay ahead in a highly competitive industry. I believe that a culture of collaboration and open communication greatly helps to reach a common vision and achieve shared goals.
And lastly, a strong sense of ethical conduct should guide all decisions as this is key to earning and strengthening the trust of all of our stakeholders.
Could you elaborate on how the global semiconductor shortage has impacted the automotive production landscape, especially in the Indian market? What specific challenges did Renault Nissan Automotive India face due to this shortage, and how did it impact your production capacity and schedules?
The shortage of semiconductor chips had a deep impact on several sectors including the automotive industry. The semiconductor shortage itself stemmed from various factors, including a huge rise in demand for semiconductors in consumer electronic devices such as laptops. This was partly a result of the increased adoption of remote work and online learning models during the COVID-19 pandemic. Moreover, the pandemic disrupted logistics and manufacturing supply chains across the world. As pandemic-hit industries, including automotive, witnessed a surge in demand for semiconductor chips in the post-COVID recovery phase, the shortage of semiconductors was felt even more acutely, and this led to several knock-on effects in manufacturing and delivery to customers including in automotive production. During this dynamic period, RNAIPL closely monitored the global semiconductor shortage situation and implemented several strategies to mitigate production disruptions.
In that case, how Renault Nissan Automotive India has successfully mitigated semiconductor shortages and maintained a consistent production rate?
RNAIPL undertook several strategic measures to safeguard our production volumes and ensure that were able to deliver on customer commitments despite the semiconductor shortage.
One of the first action items that we undertook was to create a strong cross-functional team across the organisation with various departments such as product development, R&D, Marketing, Sales, Purchasing and Supply Chain - to identify and develop alternate solutions. The uniqueness of the cross-functional team was that it operated on a global and regional level allowing our teams across the world to collaborate on a holistic basis and also have more meaningful and impactful negotiations with suppliers helping us to secure appropriate allocations on a long-term basis to meet the needs for our production plans.
Thanks to prompt action and collaborative working, we were able to continue to protect our production volumes and at the same time introduce new variants in our product mix within a record time during the semiconductor shortage offering more choice and value to our customers.
Were there instances where you had to re-evaluate supply chain strategies or modify production processes to overcome the semiconductor shortage? How did these changes contribute to your operational resilience?
Given the potential serious impact of the semiconductor shortage on our operations, we undertook a global collaborative approach to manage the situation. One of the key changes that we implemented was that we made direct contact with semiconductor manufacturers (earlier this was directed via parts suppliers) to ensure that we could secure the necessary volumes for our production needs. The learning was that while previously we could focus only on our Tier 1 suppliers, the semiconductor shortage brought our attention to the fact that we needed to engage with our Tier N suppliers all across the value chain. This strategic shift strengthened our supply chain and ensured the stability of production.
Continue reading on page 2