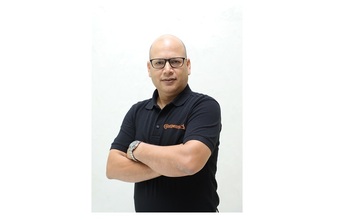
Has Covid-19 put you through the toughest leadership test of all time?
COVID-19 has undoubtedly brought an unprecedented situation upon the whole world. In a way, it is one of the biggest and most stringent tests for leadership across the industry. Many name Covid-19 as the black swan event which hit mankind in multiple decades.
While being part of the industry, we are equally impacted by this pandemic. However, at Continental, we are continuously working with all our stakeholders, including our employees, suppliers, and customers, to best manage the situation.
During this time, our primary focus has been the safety and health of our employees. At the very outset, Continental provided a work from home option wherever possible and took all necessary steps to ensure a smooth transition of work to manage business continuity topics. We have also been in close touch with our customers during the lockdown, continually understanding the changes, operating procedures, and their requirements, which f-tracked our operation resumption in a phased manner. Also, we have been meticulously following government directives and regulations on COVID-19, ensuring we are fully compliant with the law and maintaining a high degree of safety for all our employees and business partners.
Once the government relaxed the lockdown regulations for the manufacturing sector, we gradually resumed our operations with 20-30 percent of our workforce at our manufacturing plants and partly aided by the automation processes that were already in place. We not only followed the regulations established by Government authorities but in parallel also aligned with Continental global standards and guidelines to handle the pandemic. We have also implemented social distancing in all workplaces, including the shop-floors and canteen areas.
Our Industry 4.0 standard manufacturing facilities are equipped with various smart factory features, which support the resumption of work seamlessly. Apart from resuming the production, our highest priority has been to secure the supply chain and to meet the customer volumes demand. The automotive supply chain is one of the robust, fast-evolving, and lean processes across industries. Our ERP systems are integrated globally across countries and regions, which help to retrieve information quickly and integrate demand management starting from OEMs and automatic discharge of orders etc. This also reflects any changes instantly, ensuring accuracy and allowing us to respond to demand changes in a short time. Additionally, our supply chain is spread across the globe, and we are not one region dependent. Our well-equipped inventory management and warehousing help us with optimized processes to serve our customers and markets.
What do you think is more important for a leader in times like these - to be plan-driven or to be purpose-driven?
Both approaches have their own merits. Plan driven leadership, being traditional, specifiable, predictable, and process-centric, requires extensive and meticulous planning. It's more on the command and control style of leadership.
On the other-hand, purpose-driven leadership is popular among many business leaders who align the aspects of running their organisation with the core values and beliefs. Leaders who follow the model of purpose-driven leadership believe deeply in a cause, focusing on purpose before profit, which primarily motivates their decision-making. Purpose-driven leadership attracts and engages employees.
However, in times like these, we can't just pick and choose any one style. We need to be agile to the changing market demands and conditions. The best approach would be a combination of agile, purpose, and plan leadership to derive the most in the current times.
Any crisis calls for being resilient in the face of growing difficulties. But moving ahead also requires experimenting and the ability to take risks. How does a leader balance between these two seemingly opposite ideas of being resilient and the ability to take risks?
As mentioned earlier, leadership in such times is all about agility and adapting to situations quickly. Taking ownership and accountability during these testing times is an essential reflection of the right leadership.
From the very beginning of the outbreak, we at Continental have been closely monitoring and adapting to the fast-changing situation. Virtual war room meetings tracking the customer project status and supply chain topics were running round the clock. A complete switch to a virtual workstyle is not possible for a manufacturing-centric technology company, but we are indeed considering these options with a significant increase in future times.
The power of proactive, transparent, and engaged communication during these tough times, not only with employees but with all stakeholders, is unparalleled. It takes a great deal of consciousness from the leadership amid crisis and upheaval to maintain a balanced view that is neither too negative nor overly optimistic.
How do you view digital transformation for your organization in the New Normal?
Continental strongly believes in digital transformation, including smart and automated services. We are implementing Industry 4.0 processes across all our plants worldwide, which includes Artificial Intelligence, IoT, 3D Printing, AR in product development, and process automation.
At our Bangalore plant, we have already implemented Augmented Reality (AR) for remote assistance and problem-solving, Automated Guided Vehicle (AGV) for material movement on the shop floor, Artificial Intelligence (AI) for facial detection of quality inspectors. We have also implemented Cobots in our plants. Collaborative Robots or Cobots are designed to work alongside and together with humans.
With the help of these technologies, we can enhance the productivity and efficiency of the workforce and our operations. This has also enabled us to challenge the traditional way of working and have started implementing newer innovative ideas. Planning is underway to adopt several other technologies like E-Kanban, automatic replenishment, AGVs for automation in the warehouse, E-Jidoka, Augmented Reality (AR) for remote assistance, and problem-solving, AI for facial detection of quality inspectors, etc. A low-cost automation concept called Chaku-Chaku has also been adopted to help us improve the efficiency of our production lines. We are again using IoT enabled sensors and devices at our plants for predictive maintenance.
Your outlook for the Indian manufacturing industry?
Even before the outbreak of the pandemic, the automotive industry was sluggish for almost 18 months. With the new regulations and increased insurance cost, the acquisition cost went up, impacting the market demand adversely. Additionally, liquidity issues and overcapacity topics worsened the situation resulting in overall lower consumer sentiments. Currently, the industry is going through a very challenging situation. While there are some green shoots visible, however, a full recovery would take time and will heavily depend on the government policies and initiatives. With current visibility, it would take anywhere between 3-5 years for the automotive industry to reach the 2018-19 levels. On a positive note, with the changing consumer behaviour and preferences, there may be new opportunities opening-up with the need for new business models to service the changing market needs.
END