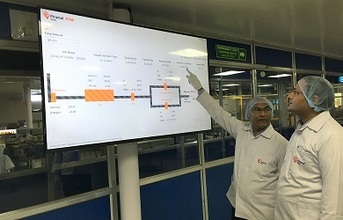
What are the key technological trends that you see impacting the way manufacturing industry works?
With sensors and cloud becoming ubiquitous, the Connected Factory or Industry 4.0 is the single-biggest trend impacting the manufacturing industry.
Traditionally, manufacturing has been a laggard in adopting technology. Specifically, in India, manufacturers are still at Industry 2.5 and by leveraging digital technologies, they can leapfrog to Industry 4.0 practices. Leveraging IoT to integrate equipment and process data into the cloud which can then be processed through AI models to provide recommendations to the shopfloor decision makers is a game-changer.
The use of AR & VR is imperative to not only provide interactive training to the employees but also to collaborate with customers is a big trend that we see.
How is digital transformation changing the manufacturing industry in terms of operations, strategy and overall business?
We can already see disruption in banking, retail, hospitality industries where start-ups are biting into the market share of large legacy companies. In manufacturing industry, the product-as-a-service model has disrupted the industry where the new model is cannibalizing the traditional model. For a process industry like ours, countries like India and China had an advantage over developed countries in terms of labour arbitrage. With Industry 4.0, where robots and AI are running the show, many of the manufacturing activities have started moving back to these developing countries. If Indian manufacturers do not adopt a digital-first approach, they will get disrupted.
With the dynamics of technology changing rapidly and regularly, how would you describe the importance of digital skills and digital training?
There is an immediate need to upskill the talent within the factories to augment the skills rather than replace them. Today, the most important action is to invest in capability building and cultural change. Upskilling in areas of analytics and digital technologies will prepare the workforce for the changing environment and make them ready for future learning - thus keeping them relevant.
Also, working alongside technologies such as AI & robots will enable workers to focus on more value-added activities such as analysing the data, collaboration and innovation. They need to understand the changing dynamics of their role and embrace continuous learning and change.
What is Piramal Glass doing in this context?
While we have built an entire ecosystem of partners that can provide us the skills in Analytics, IoT, Cloud & Security, we firmly believe that our employees need to be upskilled to become future-ready.
We have undertaken a massive eLearning program where we are training employees using multi-channel technologies and interactive learning modules. We have also rolled out a unique innovation management program which enables crowd-sourcing of ideas from employees using gamification, mobile and analytics to manage innovation from concept to implementation. We are also piloting the use of Augmented Reality and Virtual Reality to train our workers.
Study tours for leadership to start-ups and technology experience centres, road shows across all the plants to spread digital awareness and organizing start-up booths at our offices are some of the initiatives undertaken.
How can the industry work with the academia to make students future-ready in this context?
With India slated to become the single largest provider of global talent with one in four graduates in the world being a product of the Indian education system by 2030, there is a strong need to upgrade the capabilities of the Indian universities in areas of digital technologies.
Incubation of start-ups is one of the major areas where industry-academia collaboration will benefit both greatly. Another area we are working with leading engineering institutes is for training our employees in analytics, innovation and design.
Thus, the industry stands to gain much more by collaborating with academia.
END