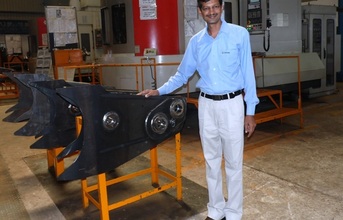
The efforts undertaken in the first phase received appreciation from the customer as well as the CII mentor. This obviously gave a big boost to the team's morale and increased its involvement and dedication. Everyone now worked towards improving the plant in every possible way.
All machine stands were modified to reduce operator movement / space saving as well as maintenance friendly. Input / Output conveyor was installed at the loader tower area and the RM & FG Storage was moved from the shopfloor to the outside gallery. This resulted in a whopping space saving of 2,560 sq ft on the shopfloor.
"We further enhanced the 5S of the plant as well as overall team work. The Plant started conducting regular problem analysis resulting in Kaizen implementation. This reduced break downs, drastically decreased rejection (with some of the related problems getting eliminated) and increased productivity. We made savings in the lighting area as well. Importantly, the overall plant appearance and ambience improved," Agarwal adds.
With the huge success in Phase I, the team under Agarwal's leadership implemented the second phase from January 2013 to September 2013. This included having the Sun Rise meetings, daily loss time analysis and Kaizen Implementation.
"It was followed by improving the OEE (Overall equipment effectiveness), identification of CTQs (Critical to Quality parameters) & the related SPC (Statistical Process Control) as well as monthly cost of poor quality & its analysis." The plant also implemented tool cost reduction by looking at various options like drill & tap re-sharp, re-coat, order scheduling, advantage of yearly sales promotion schemes from cutting tools supplier and alternate sourcing of capital tools. With training from CII, BEE, GEF and WB, energy saving drives were also implemented.
(Continued on the next page)