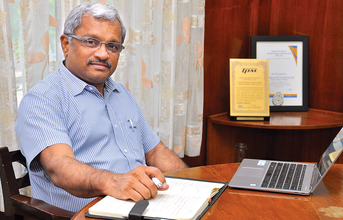
Production is supported by a sophisticated Research & Development infrastructure, with machines that simulate application scenarios very similar to customer locations. Grinding optimisation sensors and algorithms help in creating products which can be readily ported to the customers needs.
CUMI has also developed capabilities to produce a number of important adjacencies for the market, such as the Non-Woven products - industrial and home care, Power Tools for a variety of applications and Metal Working Fluids for grinding as well as for machining applications.
The Electro-Minerals Division, based in the state of Kerala produces the abrasive grains that are used to manufacture abrasive products as well as a range of other applications. It has a total capacity to manufacture 20,000 TPA of Brown Fused Alumina, 10,000 TPA of White Fused Alumina, 11,000 TPA of Zirconia and 80,000 TPA of Silicon Carbide - majority of which comes from Volzhsky Abrasive Works in Russia. CUMI has also invested in facilities to produce a wide range of High Performance friable, semi-friable and ceramic grains for specialised applications.
The Ceramics division has its footfall in Hosur and Ranipet. The Hosur facility has the capability to produce a range of customised wear resistant products for coal washeries, mining and power industries and metallised ceramics product for the high voltage electrical transmission with advanced manufacturing facilities including robots in the manufacturing and inspection lines. Other advanced applications include ceramics for solid oxide fuel cells and critical components for electric vehicles. The Ranipet facility houses the Super Refractories and Prodorite businesses - providing thermal, wear and corrosion lining solutions to the power, steel, cement and a host of other industries as well as producing complex, pre-cast composite products for industrial applications.
What are the key trends in abrasive technology and how is CUMI placed in this regard?
The abrasives business has been witnessing a change in application of its products in the industry - moving from heavy material removal operation of grinding to finishing; manual to machine operations. Higher operating surface speeds, faster feed rates, better fluid delivery systems, and cutting edge dressing mechanisms have been some of the highlights of the new age machine tooling systems. Additionally, the material surfaces have evolved from Mild Steel to High Speed Steel, Metal Alloys, Glass, Ceramics and Composite Materials, which has opened up new opportunities for CUMI to improvise and develop a whole new range of abrasive products.
Keeping with the trends, CUMI has invested prudently on facilities producing High Performance Grains - Semi Friables, Microgrits and Ceramic Grains (being one of the only three companies in the world that produce ceramic grains), which have been used to develop products that provide superior precision and finish, as demanded by the market.
With the rapid growth of sophisticated machine tool systems, the understanding of grinding has improved in the last few decades. From merely the number of parts ground, the performance of today's grinding wheels are evaluated in terms of the total system productivity. To address the high speed and high productivity requirements of our customers, CUMI has designed a range of fiber-reinforced lightweight wheels that are capable of being operated comfortably at very high speeds (125 mps) with better stability and reduced power consumption for better metal removal rates.
Leveraging it's people's technical bandwidth along with it's six DSIR approved R&D labs, CUMI is also building IOT capabilities to support the Industry 4.0 revolution by venturing into the digital space with significant progress in designing sensor and microchip embedded products that communicates with systems and smart algorithms to control the process real time.
You also have diversified presence in other segments. Please briefly tell us about the same.
Over the years, CUMI has emerged as trusted brand providing comprehensive surface engineering solutions, by adding stateof-
the art manufacturing facilities serving products in the Industrial Ceramics, Ceramic Fibres and Super Refractories space. The Ceramics business offers products which harness the heat resistance, wear resistance and insulation properties of ceramics, with technology being niche and key entry barrier. These products cater to critical and demanding applications in thermal power plants, material handling, coal washeries, cement, steel, food processing, mineral processing, electrical and electronic industries among other industries.
CUMI is also a significant player of Super Refractory products in India, serving the upper segment of the refractory market. The Super refractory Division manufactures two different forms of the product (fired refractories and monolithics). The business caters to the sanitaryware, carbon black, iron and steel, power, HT insulators, ceramic tiles, ferrous and non-ferrous industries, primarily in heat resistant applications.
CUMI's Electro Minerals business itself has built capabilities of producing a wide range of specialised grains that find use in diverse applications, emerging as a global player in the segment, rather than just supporting its Abrasives business. Additionally, CUMI has actively partnered with firms that have added value to their core offerings - JVs with Sterling Abrasives which specialises in abrasives for food processing, Wendt GmbH of Germany for Diamond and Cubic Boron Nitride bonded Super Abrasives and Morgan Thermal Ceramics UK for ceramic fibres and modules for thermal insulation.
(Continued on next page)