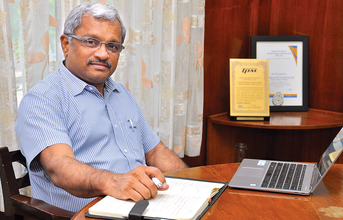
Can you give us an overview of Carborundum Universal Ltd (also known as CUMI) in terms of its legacy, business activities and market standing?
CUMI is an integral part of the Murugappa Group. It was incorporated in 1954 as a tripartite joint venture between Carborundum Co., USA, Universal Grinding Wheel Co. Ltd., U.K. and the Murugappa Group. Since its inception, the company stays committed to serve the manufacturing industry by building capabilities in the material science space to address a diverse range of engineering products - emerging as a key player in India's growth story.
The company pioneered the manufacture of Coated Abrasives and Bonded Abrasives in India in addition to developing capabilities in the fields of Super Refractories, Electro Minerals, Industrial Ceramics and Ceramic Fibres. Today the company's range of over 20,000 different varieties of abrasives, refractory products and electro-minerals are manufactured in over 25 locations across various parts of India and other parts of the world. CUMI has a leadership position in the Abrasives and Electro Minerals business - having fully integrated operations - from mines to end product. In the Ceramics and Super
Refractories business, the company has been producing niche, customised products, as per market trends, with a dominant portion of its sales coming from exports.
Today, the company believes and works towards sustainable development. In line with CUMI's sharpened purpose of Making Materials Matter we make and offer products to improve productivity, quality and sustainability in the industry.
We understand that CUMI is one of the few manufacturers in the world with fully integrated operations. How does this help (having fully integrated operations) in addressing the demands of your customers?
CUMI's position as a fully integrated engineering materials company gives a distinct competitive advantage that allows it to provide customised and comprehensive solutions across surface engineering, thermal protection, wear protection and electrical insulation among others, to our customers in diverse industries. The company's Electro Minerals division, which manufactures a product line of fused alumina, silicon carbide, sol-gel ceramic grains and zirconia grains along with micro grit specialties, support the Abrasives and Ceramics business in innovation and development of specialised new products to meet the growing diverse needs of our customers.
The addition of our wholly owned entity - Volzhsky Abrasive Works, Russia has positioned CUMI among the largest producers of silicon carbide in the world, ensuring raw material security and a favorable cost position, driving profitability in the abrasives and refractories business.
The specialty grains - sol-gel ceramic grains, alumina-zirconia, stabilised zirconia and semi-friable aluminas - many of them developed in-house and patented products offer a capability to address high performance and high precision grinding applications, that few companies can match.
Tell us about your overall manufacturing capabilities.
CUMI has 25 manufacturing locations across India, Russia, South Africa, Australia and Thailand across its various divisions. In Abrasives CUMI has a capacity to produce 20000 MT of Bonded Abrasives spread across it's manufacturing plants in Chennai -custom built, Hosur - standard vitrified bonded abrasives and in Roorkie -Thin Wheels for the distribution market. The Coated Abrasives plant in Sriperumpudur has a capacity of 16 mn sq mtr producing a broad range of Alumina, Silicon Carbide and Zirconia based Paper, Cloth and Fibre backed products in various forms - Sheets, Rolls, Belts, Discs, Flap Discs and Mops. The raw material plant in MM Nagar produces the processed cotton, poly-cotton andpolyester cloth and phenol formaldehyde resins and that are
used in the production of abrasive products.
(Continued on next page)