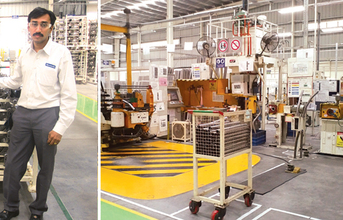
Then comes the ‘final inspection’. “Final inspection of assemblies are conducted to that all quality parameters have been meet. This becomes critical owing to the complicated profiles of our product fitments.” The fifth step is called ‘Red bins’, where scrap identification and handling is done at the source of generation itself (i.e. at process) to avoid mix-up and defect outflow. “We review every single scrap part daily and accordingly decide on temporary or permanent actions,” Bhadravathi explains. The penultimate step is called ‘Rework control’ where the parts that need to be reworked on are identified at the process and put in yellow bins. The rework is done by authorised personnel only which then sent to the quality control team for certification. And the ultimate step is the ‘Quick Response Continuous Improvement’ or the QRCI where in case of defect, quick actions are taken at the process stage itself and escalated for solving the same permanently. “Broadly put, our process of quality control is based on two approaches that include ‘Built-In-Quality’ and Outflow Prevention,” says Bhadravathi. “Quality is built-in at the process itself – Proper selection of equipment, good design of processes, tools, jigs & fixtures are the keys. Even if we any quality issue is identified, we have a strong outflow prevention process, to avoid defect outflow and ensure best quality delivery to our customers.” The Bangalore plant complies with the requirements of TS-16949 and is certified for the same. “Attaining customer delight is something that we take pride in and a testament to the fact is the awards and recognition received from Toyota each year for having successfully achieved and maintained their challenging quality benchmarks.” Attracting and retaining skilled workers has been a major challenge for Indian manufacturing. “Skilled manpower is the most critical resource for any industry and lack of this resource is a universal phenomenon,” agrees Bhadravathi. However at the group level, Faurecia has a very strong Employee Empowerment system and processes in place which are strictly adhered to in India as well. “At a fundamental level, Faurecia believes in empowerment of employees through better understanding of their role, communication, proper supervision, implementing of improvement ideas, improving skill level, reduce wastages and imparting better training. We have various employee engagement initiatives like employee progression, overseas training, education assistance, introducing and supporting employees to become process experts making them capable to in-turn develop skilled manpower. Other macro aspects which we look into are ensuring safe work environment and ensure work life balance, fostering positive work culture, providing growth opportunities through internal mobility and career progression.” END