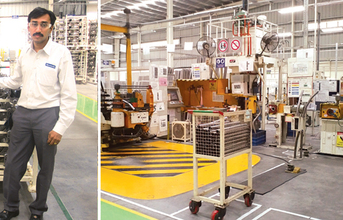
But were the equipment required and the technical know-how available in India for the introduction of these technologies? What about the availability of the skilled man power? "Yes we have the required equipments, processes and the technical expertise to introduce the technology innovations to the Indian market. In addition to this, at a global level, Faurecia identifies a team of technical experts who are deployed as a support team to various markets for manpower training and skill development. This in turn helps achieve efficiencies in designs, manufacturing processes and products."
Faurecia recently inaugurated a state-of-the-art R&D centre in Bangalore dedicated to emissions control technologies. "The Tech Centre for Faurecia Emissions Control Technology recently inaugurated in Bangalore, joins the three other existing plants in Pune, Chennai and Bangalore dedicated to the production of hot end, cold end, manifold, welded & lock-seam muffler boxes, spun mufflers, bent pipes for Ford, Hyundai, Nissan, Toyota, Tata and Cummins. The centre also supports the global engineering in the design and validation of the entire product with design, CAD, FEA, CFD and Acoustics services for programs in Europe, North America, South America and Asia."
In line with one of the major band pillars of innovation, this Tech Centre has further strengthened Faurecia's ability to deliver cleaner and more environment friendly automotive solution and technologies. "The engineers at the centre are further supported by technical leaders identified by the group who assist with constant improvement, innovation and refinement in the processes. This gives us an excellent opportunity for knowledge sharing and expanding the scope of understanding for both the teams at the plant and the tech centre. While the teams working at the plant get guidance and training on aspects of product design and development, the product designers get a better understanding of process and manufacturing challenges, which in-turn helps them in optimising their product designs."
Globally, Faurecia follows a strict quality management process and under Bhadravathi's leadership, the Bangalore plant is adhering it to a tee. "Maintaining and delivering utmost quality standards is a culture at Faurecia and is one of the major forces driving continuous developments and advancements within the system globally as well as in India. The company strongly adheres to the Quick Response Continuous Improvement (QRCI) Process for every system to ensure stringent quality management parameters in their process and products."
At a brand level, Faurecia follow seven basic rules for achieving the right quality of product. It starts with ‘OK first part', which is the confirmation on first part for quality at shift beginning, after changeover, breakdown, tool change etc. Next is ‘Poka Yoke'. "Here we focus on implementing simple mistake proof solutions for the failure modes identified during FMEA analysis and all Poka yokes are checked at the beginning of each shift and during changeover," explains Bhadravathi. The third step is ‘Self-inspection'. "At the third step, we follow the principle of "Next process is our customer, no defect outflow to next process."
New R&D centre Faurecia has recently inaugurated a new state-of-the-art TechCenter dedicated to Faurecia Emissions Control Technologies. The TechCenter is designed to accommodate about 200 automotive engineers. It is a fully-owned subsidiary of Faurecia and an R&D centre dedicated to Faurecia Emissions Control Technologies for global projects. The centre supports the global engineering teams in the design and validation of the entire product range. The technical team that consists of program development leads, specialists in durability, thermo fluids, acoustics simulation, product Design and engineering systems will enable the design and validation of Emissions Control Systems for programs in Europe, North America, South America and Asia. The TechCenter is spread over 30,000 sq ft and has a capacity to accommodate up to 360 engineers. |