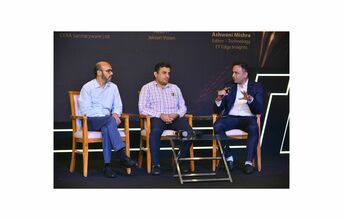
The manufacturing sector has experienced significant changes in recent years. During a technology panel discussion moderated by Ashwani Mishra, Editor - Technology, ET Edge Insights, the panellists were asked to discuss the challenges they have faced in the manufacturing sector.
Abhay Bapnaa, AVP - IT, Adani Wilmar, emphasised that technological advancements in the sector are constantly evolving, requiring companies to keep up with the pace. Over the past two years, they have encountered various end-to-end issues, including planning, forecasting, and manufacturing. Additionally, the supply chain has been greatly impacted by the pandemic, leading to constraints.
The international markets have also exhibited volatility, influenced by disruptive events in Ukraine, Russia, Indonesia, Malaysia, Brazil, and Mexico. Another external challenge has been the fluctuation of the dollar.
Consequently, understanding what and when to buy from the international market has become crucial due to the supply chain issues. Bapnaa highlighted that manufacturing also presents its own set of challenges. While things may appear fine, there are still issues to address. When they initially embarked on their manufacturing journey six years ago, Bapnaa realised that a single critical component failure could disrupt the entire production line. However, they have made improvements over the years, leveraging advanced technology and equipping components with better functionality. Bapna exemplified this with the use of predictive maintenance for boilers, which has significantly reduced downtime. The packaging process has also benefited from technological advancements, allowing for optimisation of production rates.
Furthermore, Bapnaa mentioned that his company has successfully digitised their logs. However, he acknowledged that this digitisation process has been slow. With 19 plants, each at different stages of upgrades, the process of digitaisation has been unique for each facility.
Gaurav Vyas, Head - IT, Jekson Vision, further contributed to the discussion by stating that a majority of the challenges faced by their company have been external. They encountered constraints related to raw materials and experienced supply chain issues due to the unavailability of electronic components in the market. Vyas highlighted their heavy dependence on other countries in terms of internal markets.
Nevertheless, Vyas expressed an optimistic perspective, viewing every challenge as an opportunity. He mentioned that government initiatives have led to significant improvements in the sector. However, the supply chain remains the most critical and pressing issue that needs to be addressed.
When asked about strategies to enhance resilience in the manufacturing sector and promote domestic sourcing, Bapnaa shared valuable insights. He explained that the approach to achieving resilience varies depending on the specific commodity, as the government periodically adds or removes duties. Additionally, Bapnaa emphasised the significant role played by inflation in shaping purchasing behaviours. To illustrate this, he mentioned that instead of buying oil in large bulk quantities, people have started purchasing smaller amounts (1-2 litres) to address price stabilisation concerns. As a result, when considering internal sourcing, decisions should be made with short-term supply considerations in mind rather than long-term perspectives.
Bapnaa highlighted the key contributions of electricity, water, gas, steel, and chemicals to their operations. In cases where electricity costs rise, the company diligently investigates the underlying reasons. Using approximately 19,000 data tags, they capture real-time data that enables them to promptly detect any potential defects, allowing for corrective actions to be taken in a timely manner.
In terms of logistics, the company places significant emphasis on reducing internal truck turnaround time from the plant to the destination. To achieve this, they have implemented geo-fencing technology, which helps minimise travel time and transportation costs. Moreover, AI technology is leveraged to analyse the history for external truck purchases, providing transparent analysis and interpretations.
Warehouse management has undergone significant improvements, becoming more organised and well-planned. The integration of augmented reality technology has played a pivotal role in streamlining operations and enhancing overall efficiency.
Vyas elaborated on how his company effectively utilises data to drive their operations. He emphasised the importance of data analytics in their decision-making processes. Data plays a crucial role in forecasting their business and understanding customer requirements. By analysing trends and customer feedback, they can enhance customer satisfaction and support services. Data analytics also enables them to identify areas for improvement and gain insights from past experiences. This data-driven approach empowers them to better understand customer needs and find ways to reduce costs, which is a vital aspect for any business. He pointed out that even a 1 per cent cost reduction can have significant benefits. By analysing trends and data, they can identify areas to focus on and make the overall business more cost-effective, he shared.
Bapnaa emphasised that the use of data extends beyond customer innovation, discussing the benefits of leveraging data for internal operations within the company. He specifically highlighted their implementation of digital plant maintenance processes. When servicing a machine, they analyse its maintenance history, including details such as the last service date, the responsible personnel, and the required spare parts. This knowledge helps them avoid the challenges of last-minute shortages. Interestingly, Bapnaa also addressed the issue of storing excessive spare parts in inventory. In such cases, they calculate whether it is more cost-effective to transport the parts from one plant to another or to purchase them. This approach enables them to enhance visibility and transparency while ensuring overall cost-effectiveness. The use of data in these operational aspects provides valuable insights and facilitates efficient decision-making.
Vyas added that data plays a crucial role in forecasting and monitoring consumption patterns. By analysing data trends, they are able to make urgent dispatches without the fear of material shortages.
Bapnaa further emphasized that the perspective on data has undergone a significant transformation. Unlike the traditional approach of using spreadsheets, the amount of data generated by each machine is now substantial, necessitating the development of new methods of presentation. With such vast quantities of data, an alert-based system becomes essential. This system optimises data usage by highlighting areas that require immediate attention. Bapnaa suggested implementing an 80:20 system, where the top 20 percent of pressing matters are flagged in a red-yellow-green fashion, with the red items demanding urgent attention.
During the discussion, the panelists delved into the growing security challenges associated with technology. Vyas provided insights, emphasising that security is a significant concern for everyone today, regardless of their location or industry. He acknowledged that it is difficult to claim absolute safety and security in the current landscape. Vyas identified internal systems, particularly employees, as a major challenge in terms of security. He highlighted the importance of employee skill sets and understanding, noting that laypersons often have access to servers and data centers, making them potential vulnerabilities.
Vyas stressed that threats often originate from end users, posing a significant challenge in keeping them updated and providing them with the necessary technical skills. Equally important is educating them on what not to do to mitigate risks. He mentioned that even educated individuals fall victim to various frauds and security breaches. While data centers themselves are secure, the primary source of mistakes and vulnerabilities is often at the user level, creating a significant challenge for organisations.
Bapnaa agreed that the issue of security is a critical and ongoing concern. It is no longer a one-time task of applying security patches; rather, it has become an around-the-clock issue. Any security attack on operational technology (OT) devices can disrupt production and have significant consequences. There have been cases where machine patches were not implemented properly, leading to negative impacts and costly efforts to resolve the issues.
He outlined that it is essential to take timely action in identifying vulnerabilities and addressing them effectively. This may involve monitoring and collecting data to identify potential black holes or weaknesses in the system. In some cases, seeking external expertise and adopting an outside-in approach to security can be beneficial, according to Bapnaa.
In response to the audience's question regarding abiding by government rules, approvals, and standards when implementing a new technology without a ready-made rule book for regulators, moderator Ashwani Mishra addressed the issue. He highlighted the presence of various regulators who come into the picture whenever a new technology emerges. Mishra specifically mentioned the example of AI, where regulators often question the decision-making process or the basis for granting loans based on AI outputs. The regulators scrutinise the technology to ensure that biases are not present, particularly from a banking perspective.
Bapnaa further emphasised the importance of conducting pilot tests before fully adopting a new technology. Bapnaa highlighted that conducting a pilot provides a sense of confidence, not just for the implementers but also for the management, as it allows them to visualise the unknown.
Bapnaa also acknowledged the need to seek expert assistance in certain areas. For instance, in the case of boilers, they sought the expertise of individuals who possessed in-depth knowledge of the subject matter. By collaborating with experts, they were able to identify the possible reasons for failures and determine the necessary corrective actions. As a result, they successfully reduced downtime production by 22 percent.
When asked about the best technological practices adopted by their companies, Bapnaa shared his experience, which began with conducting small pilot tests on three machines. His company identified specific products and assessed whether they aligned with established manufacturing practices. Based on this evaluation, they recognised the importance of predictive maintenance and decided to focus on implementing it. The cost involved was approximately Rs 2500 per sensor per month, along with additional implementation expenses. However, the benefits outweighed the costs, as they were able to reduce downtime by 22 per cent.
Bapnaa also mentioned his collaboration with startups that assist small and medium-sized enterprises (SMEs) in identifying and solving their problems. He acknowledged his involvement in this initiative, where they work together to address challenges within a two to three-month timeframe, offering affordable and practical solutions.