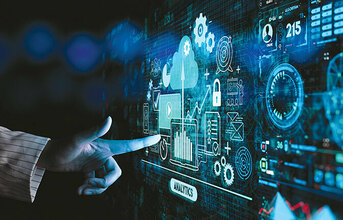
The manufacturing industry contributes about 16 per cent to the global GDP and generates nearly 14 per cent of global employment. As an essential driver in the global economy, the manufacturing industry has to evolve and adapt to the changing market dynamics continually. While the first industrial revolution saw the mechanisation of various processes, subsequent developments have been aligned towards automation, digitalisation, and data-based manufacturing.
Contemporary technological advancements and digital transformation of manufacturing units have led to ‘smart manufacturing' - a process infused with responsively designed solutions that rely on data insights and intelligence. IoT, edge diagnostics, cloud computing, analytics, Robotics Process Automation (RPA), AI and ML, and are some of the key enablers in this transition, and they either generate or rely on data. Data-based smart manufacturing is gaining relevance to the extent that the global market is expected to grow at a rate of 13.1 per cent between 2022 and 2029, crossing $658.41 billion by the decade's end. In all this, data analytics plays a crucial role. Let's see what that is.
DATA ANALYTICS & SMART MANUFACTURING
Analytics is the systematic computational analysis of data for the discovery, interpretation, and communication of meaningful insights. Data analytics in manufacturing enables industrial units to produce high-quality, customised products at more competitive prices, progressively improving customer experience. Intelligent analytics also allow companies to enhance productivity and profitability. Managers can make quick and better decisions with machine learning algorithms and real-time data analytics.
This makes real-time data generation and capture for important functions critical to the successful deployment of data analytics solutions. With real-time data available, advanced analytics can be performed, and relevant insights can be generated to support business decision-making. Data availability, accuracy, and processing ensure that manufacturing operations are uninterrupted and run as smoothly as possible. Furthermore, the key focus areas of smart manufacturing can be supported by advanced data analytics.
PREDICTIVE MAINTENANCE
Smart manufacturing facilities follow a predictive maintenance model to monitor asset conditions, and pre-emptively determine when, and how a fault may happen. Events such as machinery breakdown, improper equipment maintenance, and overrunning assets, which can create a stressful environment in the workplace, can be mitigated with the availability of relevant data insights. Machine condition data can be collected in real-time with IoT-enabled technologies such as vibration analysis, stored on the cloud, and analysed with sophisticated predictive analytics algorithms. The resultant insights empower the plant operation teams to schedule maintenance events with complete visibility of machine health. Not only does this reduce the inventory-carrying burden and improve resource allocation, but it also sustainably enhances net plant productivity.
EDGE ARCHITECTURE & DIAGNOSTICS
Edge architecture allows for the collection, processing, distribution and visualisation of data in a connected enterprise. Even when assets are distributed across geographies and are not physically accessible to operation teams, edge computing and diagnostics allow key stakeholders to monitor and maintain all assets optimally. Data analytics in edge architecture entails automated analysis of collected data at the source itself, removing any lag that may happen due to the collection of data at a centralised location. The analytical insights thus generated can translate to advance alerts and longer decision-making time for critical reliability measures.
DIGITAL TWIN
The digital twin technology allows research, production, and maintenance teams in smart manufacturing setups to use virtual representations of physical objects to test variables. A digital twin is a real-time digital counterpart of its associated asset and can only be generated by capturing complete information about the asset's condition and performance. With advanced data analytics and machine learning (ML), rapid prototyping can be done, production environments can be tested, and machine parts and sub-assemblies can be checked for functionality. This, in turn, can streamline the entire value chain and save millions by reducing production downtime.
SCALABILITY
Smart manufacturing setups must be scalable and have a sustainable infrastructure to support plant reliability objectives in all setups. This is only feasible with a data-driven, digital-first approach to manufacturing. Systematic data analytics of mission-critical processes can generate business intelligence that can guide scale-up decisions. A better understanding of the risk factors, underlying causes, costs involved, process bottlenecks, and potential ROI can be developed for diverse projects. Data analytics can also assist manufacturing leaders in planning the stages and scope for intelligent digitalisation relevant to their business model and industry.
FINAL THOUGHTS
In conclusion, data analytics is quickly shaping to be the bedrock of manufacturing strategy and operation. Smart manufacturing outfits that need to meet predictive maintenance and digital reliability goals must rely on advanced data analytics. Real-time asset monitoring, enhanced visibility of production conditions and machine health, as well as prescriptive insights for planning asset maintenance can only be possible when high-quality data is captured and analysed within the organisation.
The sooner manufacturing leaders realise this, the faster they can pivot toward a data-led strategic approach to smart manufacturing.