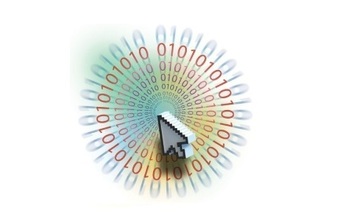
Since 2011 when Industry 4.0 was conceptualised, it has been transforming the manufacturing industry. Speaking on the same, V. Anbu, Director General and CEO, IMTMA mentions, "Internet has been transforming lives better than ever before. Like human lives, manufacturing industry is also undergoing some sweeping transformations in the technology driven world. Industries
are deploying internet of things, big data, robotics, artificial intelligence, and many more contemporary technologies to ramp up production. This is building momentum for achieving manifold growth in years to come. Smart manufacturing is synonymous with Industry 4.0 and it is revolutionizing the way manufacturing is done worldwide. The concept which first came to light at Hannover Messe fair in 2011 has now become a norm throughout the globe. It is heralding a new way of organizing the means of production by setting up ‘smart factories'. In these ‘smart factories' everything is connected. There is constant interaction between products and machines as well as between machines and machines. Humans, machines and materials are all linked together on a network and the network in turn is connected to outside world. There is ceaseless communication. The overall objective is to convert data into information and knowledge in real time to make the process productive, flexible and ensure quality. The stakes are high both in terms of technology and economically and culturally as well. Smart factories make it possible to respond to challenges of globalization and sourcing of raw materials and energy resources besides offering control over security of industrial information systems."
Seconding the same, C. P. Vyas, Head of Electrification Products, ABB India says, "The manufacturing sector has changed rapidly in the last five years. The disruptive technologies of digitalization with cloud and mobility solutions with imperatives like energy efficiency, software as a service and a churning workforce has made smart manufacturing or connected factories a stepping stone for success and customer satisfaction. Smart operation combines different elements enabling continuous monitoring of the production process through visualization of operational data, to increase efficiency and flexibility of the operational process. This is important at a time when companies are collaborating with customers to arrive at solutions which will address their issues/requirements rather than look at selling one size fits all. The smart operation line can track and monitor operational performance parameters across the entire manufacturing chain in real time. The factory also has digital lifecycle management with inter-connected automation components, machines as well as data about processes and products. This helps archive expertise and experience and collaborate with different regions and markets to arrive at optimal solutions for different geographic domains. Real-time feeds monitor the entire manufacturing process. Remote access and wireless communication with Radio Frequency Identification Devices (RFID) and connected robotics process automation solutions manage the operation process, work orders and testing parameters. This entails providing real time service to customers to intimate them before the downtime can occur, the customers can witness testing of equipment remotely in real time with the help of VR technology."
(Continued on next page)