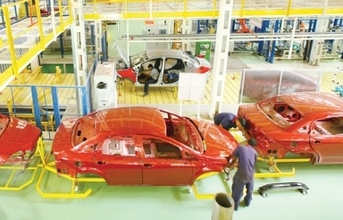
Therefore, efficiency is the ability to protect the low variable high volume products and not allow the high variable low volume product to disrupt the flow. This can be addressed by having separate lines for the low variable high volume products and switch to a process layout for the high variable low volume products.
This also addresses utilisation in multiple levels. Given the context discussed in the previous paragraphs, it is also evident that differentiated planning models would work better if the supply chain is configured at two levels: network and plant level.
Network level includes: 1) Defining appropriate stock points for aggregation of demand, 2) ensuring appropriate plant to product allocations, and 3) exploring options for producing low variable high volume products in multiple plants to address market opportunity as well as lower the risk.
Plant / shop-floor level includes: 1) Defining frozen schedules to avoid frequent changes in plan, 2) identifying stock points for consolidation, 3) lean operations to support the planning model, and 4) aligning procurement to the planning models rather than being forecast based to optimise inventory levels While this differentiated method of planning has been adopted by various organisations in different forms right from automotive to consumer products; the focus has often been on efficiency rather than flexibility.
Differentiated planning is the ability to arrive at patterns of demand in the various stages of the supply chain and aligning the planning process to these patterns which is key to achieve desired results. There is no pre-condition to this approach and is irrespective of the size of the organisation. It also does not require any significant level of investments in term of people as well as an IT enablement.
The author is Senior Manager, Deloitte Touche Tohmatsu India Pvt. Ltd.
END