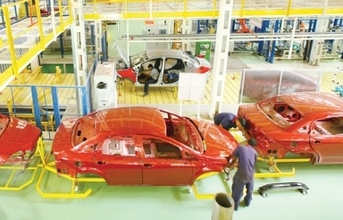
Today ‘Differentiated planning' is a compelling approach that organisations are adopting, to maintain efficiencies as well as address changing market conditions. It is the ability to use multiple planning models given the behaviour of each product category in the supply chain.
However, the challenge is in identifying the point of change / differentiation based on the demand patterns within each stage of the supply chain. To explain further, demand patterns at the market / customer level would show high levels of fluctuation, whereas when the numbers are consolidated at a regional level, the peaks and valleys reduce but still remain.
Further consolidation at a zonal / national level would present a stable demand pattern that is controllable. In this scenario, products that have a low variability in demand and high volumes would follow a batch process in manufacturing with standard quantities planned for a period of time.
But the same product may have a highly variable demand pattern in the market and, a replenishment based model (in warehouses closer to the point of sale) would be adopted with defined inventory levels to accommodate for fluctuations including the supply lead time.
Differentiated planning can also be configured within the four walls of a plant. For example, in pharmaceutical manufacturing, the same product would be packed in multiple pack sizes (10 units or 12 units in a strip) given the market requirements; therefore the plan for packing would be based on the customer demand as it is more susceptible to demand fluctuations.
However, in the preceding processes the product (tablets) can be produced in defined batches / quantities which are a consolidation of many pack size variants, and this reduces the variability in demand for those processes. The same is applicable to automotive; the engine assembly would have a different planning approach (given similarities in the engine configuration across car models) whereas, the body shop would have another approach given the external design of the car.