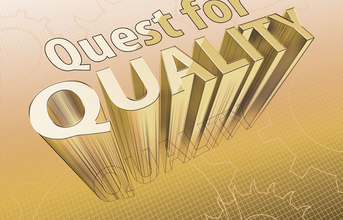
We provide intensive training to our employee by means of on-the-job and class room training to sharpen their knowledge and to upgrade their skill." Steelcast has divided its training material into six categories. Training under theoretical and on-the-job both have three categories each of basic, advance and detailed advance. "Along with the training material, we also have an effective evolution system in place whereby we can review quality of the training provided. This will help us to identify further training skill to be imparted to the employee," Tamboli adds.
Ghosh says Disa employees at all levels are owners of quality of various activities they are associated with. Every day 5S exercise of 10 minutes duration and a monthly BKW (Brisk Kaizen Workshop) involving everyone is conducted. Annual mapping of competency to assess training needs at various levels of employees is used to determine training calendar for the year.
"Every new workman joining the shopfloor needs to undergo a fixed period of training and is attached to an experienced workman to get trained. Quality circle involving concerned employees as a team, in place to find out the root cause of defective sub assembly/product."
Shakti Pumps too puts emphasis on training. "We believe quality is a continuous process. To make it happen, we need continuous improvement in systems and processes. We have a full time training & development department which conducts various training programs including trainings on quality to develop skills to maintain consistency in quality."
Shakti Pumps also has a Kaizen committee that evaluates and approves kaizen proposals and reward employees who bring it on the table. "Through this process, we are able to involve and educate employees in the quality improvement processes. Every month our Kaizen team meets and motivates employees with certificates and awards," Patidar says.