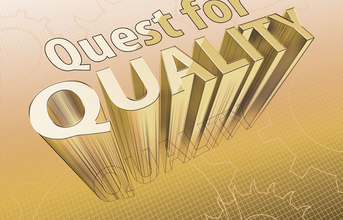
At Steelcast, quality maintenance is done through continuous focus on research & development, technology upgradation and innovative product development solution. "In the last couple of years, we have invested a lot towards quality improvement and product innovation."
According to Joydip Ghosh, Vice President - filters business & HK operations, Disa India Ltd, his company is an ISO QMS certified company and follows the Toyota World Class Manufacturing (WCM) practices to maintain product and service quality. Being in the capital equipment industry, Disa has a big challenge to customise equipment offering to suit customer need and choice.
This could result in many variations of same equipment and risk of obsolescence of parts due to wrong configuration control at engineering Bill of Material levels. "Adoption of WCM has helped Disa tremendously in keeping the shop clean and orderly, ordering, procuring and using only what is required for a particular project, eliminating the risk of wrong part fitment, etc. We have benefited in terms of reduction in customer complaints, reduction in free replacement of parts to project sites, reduction in overall project execution time, control of project cost, etc.," Ghosh explains.
An important feature of the quality systems is the actual quality checks on the shopfloor. For example, Shakti Pumps conducts inspection with the help of Special Purpose Machines at every major stage of the manufacturing process. "We also do process audit, performance tests according to specifications and final Inspection and packing audit," says Patidar. Steelcast has three main quality checks on its shop floor.
At Disa, quality checks start with vendors being trained to conduct self-inspection of parts and ensuring no product is offered to Disa, which does not meet specifications. Incoming quality check, during receipt of goods is organized depending upon the level of the supplier and his past quality performance. After the equipment is assembled, the production team and their supervisor run the same to check the dry run performance. "Final certification of equipment is done by experienced QC Engineers, who match the customer requirements as per sales records with actual equipment manufactured," says Ghosh.
Having the right systems and processes is one thing and running them effectively is another. And this can be ensured only by involving people. Tamboli says it is important to train and involve employees to align them with the company's quality goals. "Continuous training and learning are very essential for development of employees which in turn will help company in future.