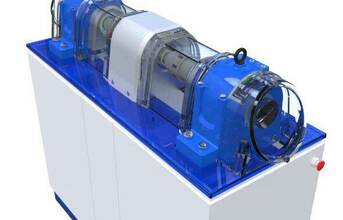
Traditional condition monitoring looks for early signs of failure by measuring vibration levels. A bearing starts to produce vibration signals when the first small fragments of steel spall off the raceway surface of the rings or the rolling elements. By the time such damage is detectable, it is likely that the end of life of the bearing is getting close - it is already damaged, and it is too late.
By contrast, our Insight programme uses bearing-embedded sensors to monitor the critical parameters that are likely to lead to an early failure, for example lubricant contamination or excessive loads or temperatures. By proactively eliminating such anomalies, the failure can be avoided. The same technology can be used in a more positive way: By verifying the integrity of an installation and giving a better understanding of the operating environment, a machine may be uprated to extend its life or power rating beyond the initial design.
Combining technology
Bearings have long been considered the heart of rotating machinery. Now, we make them the brain as well. In essence, the Insight programme puts together the technology that can monitor the actual conditions experienced by bearings in a particular application. Embedded sensors measure loads, lubrication conditions, speed, vibration and temperature using power harvested from the application environment.
Our algorithms and diagnostics interpret this data in terms of the severity of the conditions, or how far the operating conditions are departing from their original design condition. It can also identify excessive loads, duty excursions, lubricant contamination and lubrication problems so that modifications can be made to the operating conditions to avoid damage before it occurs. This package of sensors and algorithms has been named Our Insight programme because that is what it provides - an insight into the operating conditions and how those are likely to affect the reliability of the installation.
Intelligent wireless communication technology packaged inside the bearing enables it to communicate within environments where traditional Wi-Fi cannot operate. Bearings enabled with our Insight programme create smart networks, communicating through one another and via a wireless gateway to send information relevant to their condition for analysis. The gateway can be local to the machine or local to the plant. System information is either made available to the customer for analysis using our @ptitude or sent via our cloud to our Remote Diagnostic Centres. From here, dashboards and reports can be made available to the plant operator, the machine manufacturer, SKF or any other authorised person with Internet access. Real-time condition monitoring data is accessible to everyone involved. Our Insight programme gives customers more control over planning their machinery maintenance and optimising their machinery operations than ever before.