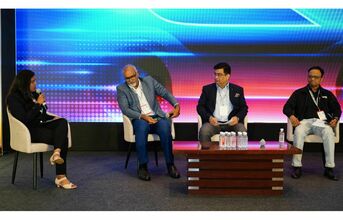
Practically, there is a need to work backwards. There needs to be a discussion with the top management of OEMs while making a business plan of metal versus plastic. Secondly, there is a need to look at rationalising global product designs. For instance, if a product design that has been successfully tested for the European market is applied to the Indian market, the associated costs would not be sustainable. It necessitates repeated and thorough CAE analysis, along with frequent returns to the research and development phase. This poses a significant challenge, especially given the existing proven design. While the OEM desires the design and performance, the second phase of costing becomes impractical.
Additionally, it's crucial to ensure that the design, engineering, and manufacturing costs are extensively localised. There need to be conversations with local raw material suppliers to maximise raw material localisation and minimise reliance on imports.
However, there's a styling challenge to address. As the glass fibre content increases, design flexibility decreases. Delivering the required mechanical performance in plastics may necessitate increasing the glass content, which could limit styling capabilities.
Complimenting this, Vilas added that the primary concern is the challenge of changing raw materials after the product's start of production. To address this, one must involve raw material suppliers at the beginning stages of product design. By doing so, unnecessary duplication of validation costs is prevented, as both OEMs and suppliers invest significantly in validation processes.
Discussing challenges, Gugale pointed out that even if technologies are accessible, the key question is whether we have the capability to adopt them. Effectively using these technologies necessitates a skilled workforce, which is, once again, a struggle in the context of India. Without skilled manpower, it becomes challenging because these processes demand precise controls, as even small changes in the process of raw metal will have a direct impact on the product. And today, when OEMs are manufacturing such high volumes, every part and every downtime count.
Expanding on the concept that lightweighting is often equated with lower cost, R.T. pointed out that while this might be possible in certain cases, it is hardly ever the norm.
Shiv highlighted the importance of considering more than just the component cost and placing focus on the net enterprise value and the net purchase value. This broader perspective encompasses aspects such as serviceability, car performance, productivity, and rejection rates, treating it as a comprehensive measure of the net enterprise value for the entire multi-purpose vehicle (MPV).
Examining the net enterprise value reveals that while the part cost may be higher by 5 per cent, considering the overall net enterprise value, which includes serviceability and performance benefits, presents a more comprehensive picture. For instance, the advantages to the OEM in terms of weight reduction, even with a 2 per cent price increase, would still result in a positive net enterprise value.
Nisha then raised a question to Gugale regarding the potential drawbacks of placing excessive emphasis on lightweight design. She inquired whether this emphasis could affect the durability of the product or lead to an increase in the cost of repairs.
Gugale responded, saying, "Definitely nowhere is it compromised." He explained that compromise is not possible because OEMs must adhere to all rules, regulations, and requirements, ensuring no compromise on vehicle maintenance costs. Furthermore, he added that by reducing the weight of vehicles through better technology, there is a likelihood of reduced downtime and fewer failures.
There isn't any penalty for end-users when using lightweight; he added that, in fact, it brings benefits. It's crucial to not think that incorporating many lightweight parts compromises vehicle safety or customer comfort. On the contrary, such choices offer more advantages, so they should not be perceived negatively.
Regarding production costs, Vilas explained that these technologies are undoubtedly more expensive than the traditional models commonly in use. Currently, high-end vehicles utilise these special materials, but for mass-volume cars like Nixon, they still rely on traditional materials.
To incorporate lightweighting for mass production, it's crucial to assess its cost viability for OEMs. There needs to be a localization of materials in India and an establishment of an efficient supply chain to reduce costs.
Continue Reading on Page 3