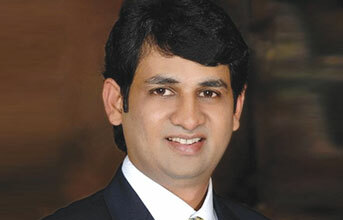
While discussing s u s t a i n a b i l i t y , several things come into our collective consciousness. Some may think about wind farms, green initiatives, recycling, electric vehicles, or even planting trees. However, sustainability goes beyond these separate concepts. It is the entirety of our efforts to meet current needs while ensuring that future generations can do the same. At its core, sustainability goes beyond mere conservation; it is also about safeguarding humanity.
In a product lifecycle, sustainability means realising the product with reduced and recyclable materials, reduced energy input, and reduced emissions during product manufacturing. Simulation plays a crucial role in sustainability throughout the entire product lifecycle. It expedites time-to-market, optimises resource utilisation, minimises product footprints, and cuts costs. Simulation accurately depicts product functionality and allows engineers to transition confidently from concept to reality. It helps industries align with the fast-paced competitive market demands of today. Simulation aids engineering teams in understanding resource conservation and emission reduction strategies during product enhancement. Beyond the design phase, simulation demonstrates how companies can adopt more efficient practices during manufacturing, utilisation, and maintenance of products.
Multiphysics simulation is like a sneak peek into the future. Engineers operate within short timeframes with limited resources. Simulation can accelerate sustainable concepts while optimising efficiency.
SUSTAINABILITY STRATEGY
Breaking down sustainability into manageable components enables progress tracking. The need of the hour is a dual-focused strategy that covers environmental, social, and governance (ESG) objectives and supports customers in achieving sustainability goals through simulation. Simulation tools accelerate the development of newer, more efficient, eco-friendly technologies and reduce waste and physical prototypes. By instilling ESG objectives into decision-making, longterm business value can be created, fostering a quicker transition towards a sustainable future.
Various industries can harness simulation as a facilitator for achieving their sustainability goals. Within the energy sector, companies are curbing greenhouse gas emissions, enhancing low-carbon energy alternatives, and streamlining operations through digital twins fuelled by simulation and artificial intelligence. Automakers are transitioning towards electric mobility while improving aerodynamics and reducing vehicle weight to extend range. In aerospace, endeavours involve exploring novel propulsion and fuel storage methods alongside advanced manufacturing and model-based system engineering. The high-tech sector leverages simulation to craft energy-efficient electronics embedded with material intelligence, fostering enhanced e-waste recovery. Furthermore, heavy industry, pivotal in crafting industrial machinery and materials, is shifting towards digital workflows reliant on the industrial Internet of Things (IoT), optimising operations, conserving energy, and mitigating pollution.
Given the widespread integration of simulation into sustainability initiatives across industries, sustainability-focused solutions can be focused into four key pillars:
The first is a ‘Clean Environment' that encompasses solutions that help customers filter pollutants from the environment, optimise energy usage, and extract carbon from the atmosphere. The second is ‘Materials and Circularity,' which revolutionises product lifecycle management by facilitating product creation, manufacturing, distribution, recapture, sorting, and reuse, thereby minimising waste in the collective future.
The third is ‘Energy Solutions,' which provides technical leverage to drive the decarbonisation of energy systems and aid customers in transitioning towards energy-efficient and renewable solutions.
Finally, ‘Manufacturing and Operational Efficiency' equips manufacturers with solutions to streamline operations, optimise material usage, and enhance reliability, ultimately reducing power consumption and emissions.
OVERCOMING OBSTACLES WITH SIMULATION:
Proficiently using energy sources, including wind, solar, hydrogen, consumer waste, biofuel, etc., requires addressing complex, physics-based challenges. Baker Hughes and LG Electronics, among others, have already employed Ansys simulation techniques for sustainable manufacturing. Simulation catalyses sustainability across the product lifecycle, spanning conceptualisation and design to prototype testing, production, operations, and end-of-life considerations.
Simulation yields numerous sustainability benefits across various aspects. Materials Intelligence initiatives encompass lightweighting strategies, compliance with regulations, sourcing non-conflict materials, and increasing the utilisation of sustainable materials and processes. This can be enabled through the suitable materials information repository. With broad coverage of material types and property data, the Ansys materials database allows users to take simulation to the next level with instant access to consistent, validated, and ready-to-use data. This will ensure intelligent material selection, optimum material utilisation, traceability, and compliance throughout the product development lifecycle.
Multiphysics Solvers mean improved designs, fewer physical tests, and reduced waste. Utilising Autonomous Vehicle Simulation leads to decreased fuel consumption, lower insurance costs, and enhanced safety measures. Implementing Design Optimisation & Digital Twins facilitates streamlined production processes and predictive maintenance practices. Regulatory Approval simulations ensure compliance, authorise materials usage, adhere to noise limitations, and conduct comprehensive risk assessments. Simulation Process and Data Management practices enable sustainability tracing, enhance process predictability, and provide better control over data access and utilisation, preserving intellectual property and fostering sustainable talent development. Model-Based Systems Engineering initiatives minimise waste, optimise product designs, guarantee meeting requirements, and accelerate speed to market. Digital Mission Engineering endeavours focus on space debris removal, optimising missions, and pioneering novel mission approaches. Companies can achieve greater efficiency, reduce waste, and contribute to a more sustainable future through these comprehensive simulation-driven sustainability strategies.
MANUFACTURING AND OPERATIONAL EFFICIENCY:
Simulation lets manufacturers plan and optimise operations meticulously, leading to more efficient material usage and better reliability. This reduces power consumption, lowers emissions, and contributes to sustainability. With features like advanced manufacturing techniques, digital twins for predictive analysis, and prognostic health management, simulation empowers manufacturers to achieve superior energy efficiency, ensure product reliability and durability, and optimise workflow processes. For example, Ansys supported advanced air purification technology startup Praan for its clean-air mission by accelerating prototype development from four-and-a-half years to 45 days. On the other hand, Atomberg, a leading high-efficiency fan and small appliance manufacturer, used Ansys simulation solutions to develop intelligent fans with 65 per cent less electricity consumption.
In sustainable digital manufacturing, particularly in sheet metal forming, the challenges of reducing energy consumption and shortening the design cycle are effectively addressed through simulation-driven solutions. Rapid decisions can be made by simulating the end-to-end forming process and evaluating formability, leading to reduced wrinkling, and thinning of sheet metal while optimising the forming process and yield. The outcome is significant: a reduction in industrial waste stemming from failed components during forming, a minimised environmental impact from inefficient processes, and an elimination of energy costs associated with physical testing. This approach enhances sustainability and improves efficiency and cost-effectiveness in sheet metal forming operations.
Simulation enables companies to conserve resources and energy and reduce emissions before physically constructing products. It plays an essential role in augmenting the speed and cost-effectiveness of environmental innovation and accelerating the development, maturation, and deployment of new technologies. By providing predictive certainty, simulation is instrumental for a sustainable future.