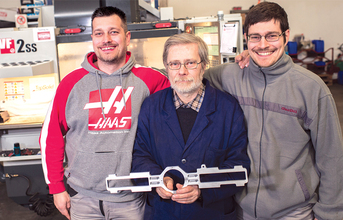
Davide claims that his early experience with Haas helped make up his mind about the capabilities of the machines, and their suitability for a growing job shop. Projects vary as much in type and industry sector as they do in volume of parts required. The company's Haas VF-2SS, equipped with an HRT210 is always busy, claims Davide. "We use this machine a lot for more complex parts - typically, prototypes. We use TopSolid CAD/CAM and programme off-line, whereas, with the ST-10, we usually programme at the machine. We're currently using the ST to make bearing housings for the Airbus A350 and Ti rear wheel hubs for the Politecnico di Torino hyper-mileage car. The VF-1 is being used to machine parts for a drone used to measure contours of the land in 3D."
Around the workshop are various other projects that the company isn't at liberty to discuss openly. One component in particular looks like the inner part of a steering wheel for a high-performance sports car. "I can't tell you anything about that," smiles Davide. "Secrecy is important for some of our customers." Good reputations are hard to come by but very easy to lose. "We've built our reputation on delivering good parts on time," says Davide, "but also for being trustworthy and discreet, at the same time."
"The auto sector is very sensitive, especially in this part of Italy. There are some big names nearby." He further said, "As our assignments become more complex, and we attract more big-name customers, we already know we will need more Haas machines; the UMC750, for example." For more than 50 years, five axis machining was simply too expensive for small to medium sized job shops like G-Tech CNC. Not anymore. "The UMC750 is an affordable 3+2 machine tool," concludes Davide. "Like the Haas machines we already own, if we buy one it will allow us to expand and build our business for years to come." And with its reputation preceding it, perhaps this family will stay in business for many more generations, as is the Italian way.
END