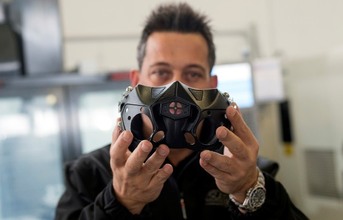
These days, Subspec is a world-leader in bespoke subsea diving systems, and has close ties and partnerships with various other organisations, including neighbouring firm, Drass Srl, which manufacturers the full gas reclaim system in which the Subspec valve is used, as well as complete hyperbaric chambers, and other systems used by commercial saturation divers.
"We make all the fittings and valves for the chambers, and the diver monitoring and safety systems built by Drass," says David. "For example, a complete hyperbaric chamber might cost a customer around €2 million. The parts we make could easily constitute €350,000 or more of that total cost. Being next door to Drass has helped our working relationship enormously. In fact, we're now invested as a partner of the company."
There's no question, Subspec is on a roll: "We're planning to open a UK office, and we have lots of ideas for new products," says David. "Perhaps the most exciting is the full diving helmet we're designing. We're still at prototype stage, but we already plan to do all the machining in-house using a Haas UMC-750 universal machining centre."
In an industry where mistakes are punished in the severest way, professional deep-sea divers are trained to get the job done, but carefully. David Marzi and Ciro Caiazzo don't take chances with the parts they make, or with the CNC machines they use to make them.
END