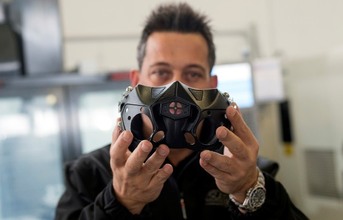
Professional deep-sea divers need to know a thing or two about technology and engineering, but they're not usually required to know how to run CNC machine tools. The founders of Italian dive equipment manufacturing company, Subspec Srl, on the other hand, have taught themselves all they need to know to make parts for some of the best and most innovative commercial dive systems available.
"My friend and colleague, Ciro Caiazzo, and I started the company in 2012," says Managing Director David Marzi. "We were both commercial divers working around the world in the oil and gas industry. We had an idea for a gas reclaim valve—we felt the industry generally was slow to develop and adopt new technology, so we thought we'd design, make, and patent the product ourselves."
During lengthy, deep dives, professional divers use very large amounts of breathing gas mix. A gas reclaim system recovers helium—an expensive constituent of breathing gas that would otherwise be vented and lost to the atmosphere. A gas reclaim valve is a critical component of the gas reclaim system, and is subject to high rates of wear and corrosion.
The responsibility for running Subspec's CNC machining operations falls to Technical Director Ciro Caizzo, "Our main machine is a Haas VM-2 mould maker," he says. "Our products - typically valves - are critical features, and can mean the difference between life and death if they don't work flawlessly and reliably. We wanted to be 100 percent sure the parts were made to our standards, and to eliminate the possibility of quality issues. That's why we bought the Haas machine - so we could take control and do all the critical machining in-house. Most of the parts we make are stainless steel, and tolerances are tight; 0.02 mm is common for an O-ring seat. The VM-2 table has a grid of T-slots in X and Y, which gives us flexibility for holding all the different sizes and shapes of parts we machine. We also do our own laser welding in-house, and a few other processes, such as vacuum casting."
(Continued on next page)