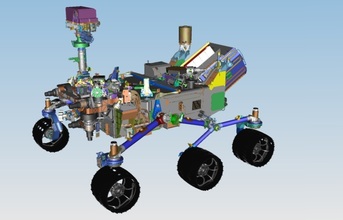
Rover Deployed Side - CAD
Computer Aided Engineering (CAE) and, in particular, Finite Element Analysis (FEA) tools are used by many manufacturers to check designs before they are used in the field. This helps ensure that the products made are fit for purpose and handle the rigours and stresses of harsh environments.
But there are some designs that, for one reason or another, have to be right first time. For anything that's sent up into space for example, there is no going back and fixing things that might go wrong, and this is where you need some really powerful and accurate simulation with advanced analysis performed up-front.
The challenge
Testing products and designs that are going to be used in places far outside the constraints and norms of daily life is difficult. Additionally, recreating these stresses and scenarios is complex, but given the nature of these deployments, there is only one chance to get it right and no margin for error.
To meet these modern challenges, manufacturers are constantly looking to expand the performance limits of their structures to enable lighter and more capable designs, at the same time as delivering cost savings for the manufacturer and the end-operator.
Simulating how real-life events will impact these designs has proven to be a key asset in these efforts. This technology enables engineers to explore different designs and materials to arrive at an optimal design by reliably predicting when these designs will fail to meet the rigorous safety margins.
Demanding environments
Whether it's the vacuum and near absolute zero temperatures of space, or the heat and friction of re-entry or the pressures of the bottom of the ocean, these projects require meticulous planning and precision performance.
It's not enough to test individual parameters such as heat, friction or stress in isolation. Rather, any simulations need to be able to replicate these conditions in conjunction and with a variety of different combinations.
(Continued on the next page)