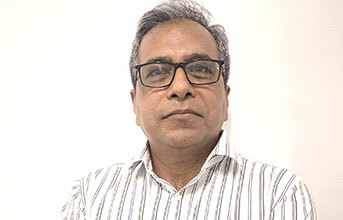
In 1976, Dr G Venkataswamy (Dr V) decided to "eliminate needless blindness" and started the 11-bed hospital staffed by four medical officers, called Aravind Eye Care. But he soon realised that to achieve his vision, the current way of working would not be enough to serve large volumes of people and making patients wait was something he did not want. So, he decided to bring in the unique assembly line approach and improve his productivity tenfold. Today, Aravind Eye Hospital is the world's largest eye care provider (4.5 lakh procedures in a year and to top it all, it does not charge 50 per cent of its patients.
So, what does ‘De-skilling' have to do with this? A lot provided the principles are understood before implementing the practices. How and what could an eye hospital learn from an assembly line and implement it to get ten-fold gains?
Let's change our perspective and see what McDonald's has done to maintain the same standards globally, considering people working in any outlet are not "cooks or chefs." So how is it that the French fries are the same, irrespective of the outlet you go to? Well, that's the practice of de-skilling at work. So, what did they de-skill, and why?
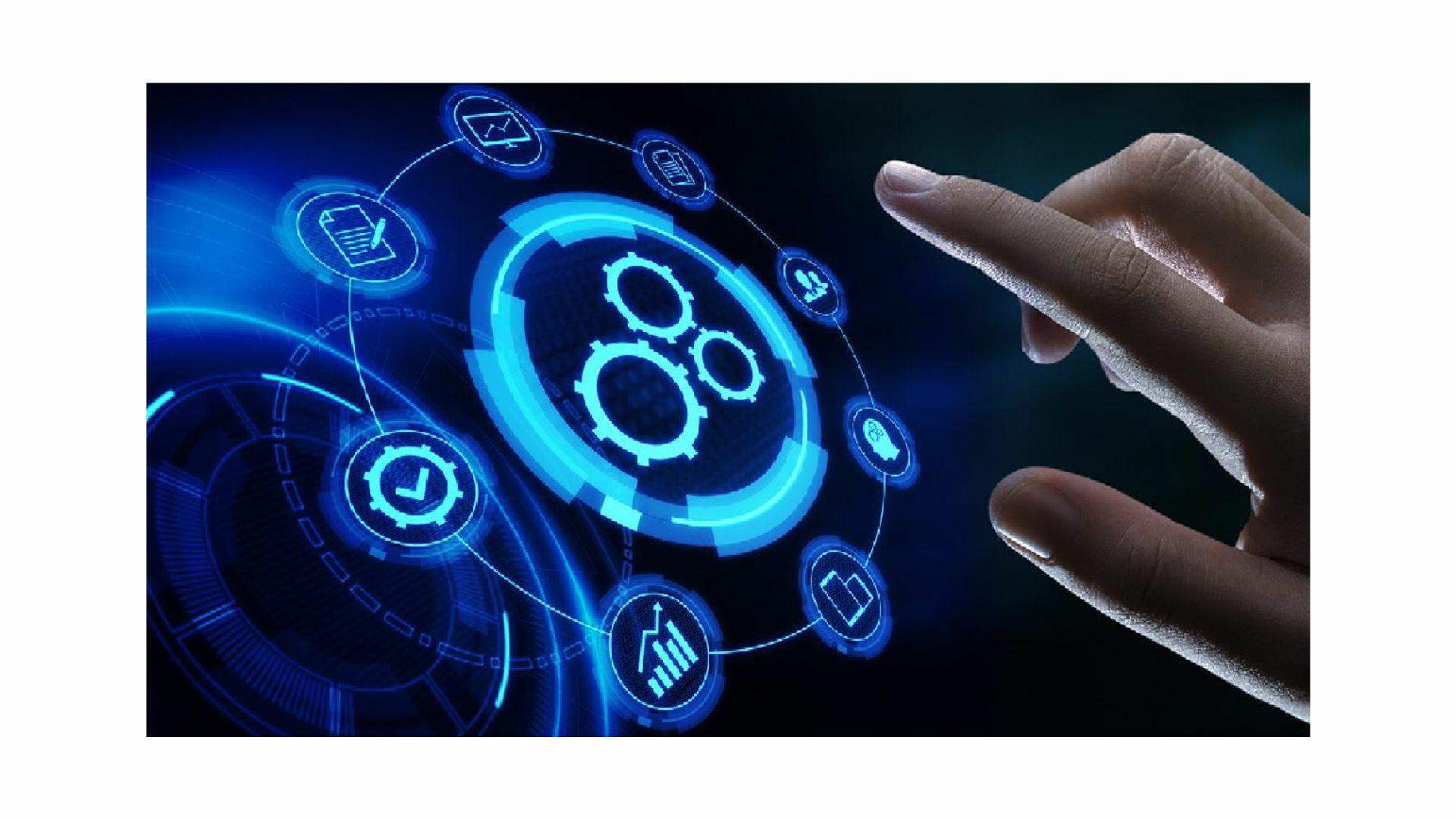
Both entities above essentially did two things: first, they managed to segregate the "style" of work and "standard" of work and second, they separated the "physical work" from the "thinking work." Once these two were done, the process steps were standardised (either by digitisation/mechanisation or automation) to such an extent that they could squeeze the "variability" out of the process to the maximum. A consistent, sustainable, repeatable, and continuous process remains when you do all that.
So, when Aravind Hospital placed two patient beds side by side and asked the doctor to make the "cut" to finish the operation on one bed, while the other patient was getting prepared on the bed right behind them. It was an example of separating the physical work of "setting up" the patient and the "thinking work" of the doctor. Hence, the "doctor" was only doing what they were supposed to and not fatiguing out doing ancillary work. In parallel, the "physical work" was divided into small standard actions and standardised to the extent that even a fresher or semi-trained nurse could set up the bed with minimal training. Bingo! De-skilling at work. An additional benefit was the reduction in training time and easy replacement and/or easy job rotation.
A simple way to look at standardisation is to remember the principle of adjustments to settings, i.e. you don't tell people "how to" do it but rather "what to" do. For instance, in earlier days, when you went to fill petrol, the person used to fine-tune the counter to the last paisa or millilitre (ml) and hence had to stand there all along to ensure that. But now he sets it to the amount you want and goes out filling some other car (unless you are getting your tank full). He is more productive now, as he does more work simultaneously with less fatigue.
Similarly, suppose you spend time absorbing the work of any McDonald's outlet. In that case, you will realise a few things; for instance, the alarm goes off when French fries are done (no one needs to monitor it), and the movements of each member are limited and standardised to reduce fatigue and wasteful movements.
The dispensers are click-type and dispense precisely, the same amount of salt/cream, every time. Ever noticed the burger pack, it is designed to work in parallel while making the burger, so information sharing is de-coupled. Screens are used to transmit information (no dependency/collaboration required), the pack has an easy lock, and there are so many other examples of de-skilled work.
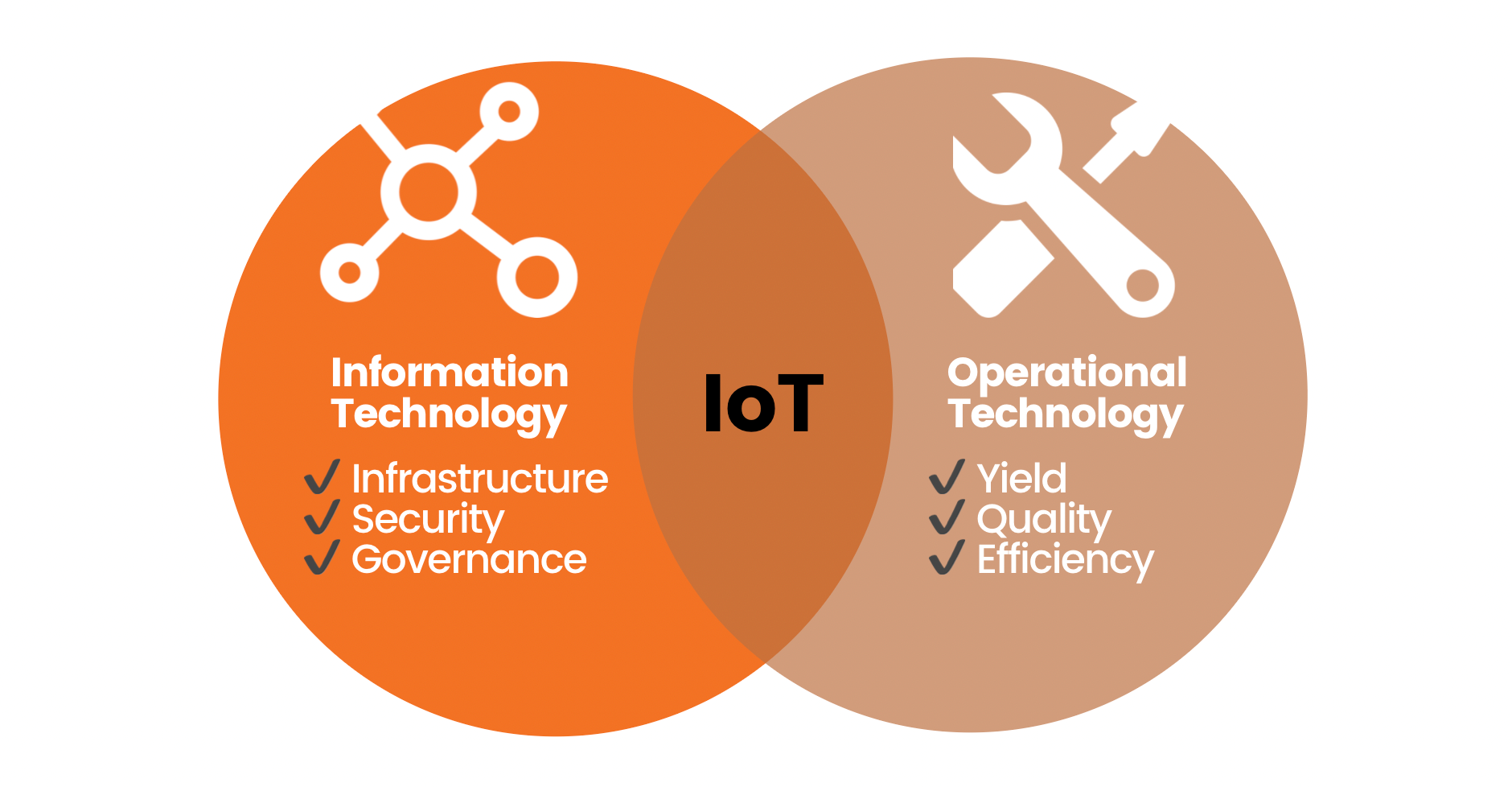
SO HOW DOES DE-SKILLING HELP?
Well, here are a few benefits:
• It helps get supervisory control over the process; in other words, it allows you to decide the rhythm of the process rather than leave it to different people's different skills to run the operation. So, if you control the process, you also control the result.
• It enables you to identify different solutions for manual and thinking work (digitisation / AI) to simplify the process further.
• It helps you reduce training time for any process and reduces the chances of error substantially.
• It enables you to disperse your value adders across processes/sites etc. You get to ensure that "adjustments" do not become "skills" and that style and standards are well segregated.
• It increases capacity creation by doing away with ancillary and incidental activities and saves time. Ancillary and incidental activities tend to increase fatigue and, hence, reduce productivity.
• It sets your direction towards a consistent, sustainable, and capable process.
• It helps you identify a new set of value-added skill requirements and upgrade your process rather than just managing and maintaining the ageing process.
Often seen as a negative trend in the workplace, de-skilling, on the other hand, offers some benefits. For example, de-skilling can allow companies to reduce their labour costs and increase profits. It also improves efficiency and simplifies processes. The term de-skilling refers to the replacement of human labour by machines or automation, such as a worker in an assembly line. This means they will no longer need to perform the task but may still be required to maintain and operate the automation equipment, requiring a higher level of skill.
So, as you get onto your de-skilling journey, you will eventually hit your current technology barrier; that's the time to move to new technology and start this process again to continue your productivity journey.
As the de-skilling score reduces (the lower the score, the faster the learning), the red curve and productivity increases (the green curve). However, productivity increase will present a barrier concerning the current technology used. Hence, when a technological barrier is reached, it's necessary to consider new technology. However, the selection of technology highly depends on the variability of products and processes it has to manage. Therefore, a trade-off must be worked out while crossing the current barrier and selecting the next.
It's a never-ending journey, and now with technology driven by AI and ML, the challenges are increasing for selecting the right one and exploiting it to your advantage.