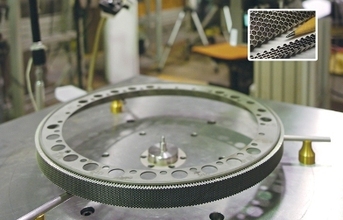
Avant-garede machine design
SRMS is a high precision optical measurement system which is designed for measuring the roundness, flatness and PCD (Pitch Circle Diameter) of the holes on the seal rings by switching modes on its remote control pad. This system comprises three main modules: the rotary table, the integrated optical measurement head on main console and the software console.
Ng explains: "Our SRMS' measurement head features a built-in high-accuracy class 3R Laser Displacement Sensor (LDS) and an industrial camera, which moves horizontally (X) and vertically (Y) on the main console. The laser takes measurements for both internal and external roundness, while the camera takes images of the holes around the PCD and provides remote monitoring of the LDS laser spot position. This results in the improvement of measurement precision which the probe system could not provide."
The seal ring for inspection is placed by the operator on the rotary table, providing a placement tolerance of ±2 mm through the built-in auto-centering function. The operator then selects the corresponding ring type from the library and starts the measurement. The measurement head remains static to capture and send the data to the software console for processing. Every individual measurement reading from the head is coupled with corresponding rotary table positional data from the encoder, and then post-processed to compute a holistic geometric measurement of the sample.
Enhancement of machine tool reliability
Other than SRMS, which uses Renishaw's encoders, HAESL also uses Renishaw's QC10 ballbar to assess their machine tool performance: "The ballbar allows us to track and identify problems earlier to enable preventative maintenance. This helps to minimise production downtime and ensure the accuracy of parts produced. We are currently considering upgrading this to Renishaw's latest QC20-W wireless ballbar system which offers more advanced features such as Bluetooth wireless connection, ‘partial-arc' testing and single setup for three-planes testing," says Eric Lau.
HAESL also uses Renishaw's TP200 high accuracy touch trigger probe with the PH10 motorised probe head system on their co-ordinate measuring system (CMM) for part inspection. Raymond Siu explains: "Inspection is a highly important and vital process in the aero-industry. Renishaw is the undisputed market leader in CMM probing technology and is undoubtedly our first choice."
END