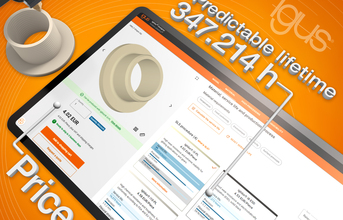
igus introduces a new addition to its 3D printing services, now offering the ability to predict the service life of custom-made special parts within seconds. Customers can simply upload their STEP or STL files, calculate the service life, choose the appropriate material, and place the order. The parts will be shipped within three days.
With 30 years of experience in plain bearings, igus uses high-performance plastics developed through injection moulding. When specific wear-resistant parts are needed beyond the standard range, 3D printing comes into play. Whether it's individual parts or small quantities, igus can quickly print and deliver the right special parts within three days. Various processes and materials, such as rapid tooling, filament, laser sintering powder, and liquid resin, are used for this purpose.
The online 3D printing service is user-friendly. Customers can upload their product file and explore production options, materials, and finishes. The tool also provides cost, feasibility, and delivery time information. By integrating service life calculations into the 3D printing service, users can now make more informed decisions about material selection, as stated by Tom Krause, Head of Business Unit Additive Manufacturing.
The reliability of igus' service life calculations is backed by extensive testing in their 3,800-square-meter laboratory in Cologne. With 11,000 abrasion tests performed on 450 test rigs annually, the results show that 3D-printed parts made from iglidur plain bearing plastics outperform conventional plastics in both turned and injection-molded parts. The service life can be up to ten times longer and even up to 50 times longer than other 3D printing materials. With over 50 iglidur materials for injection molding, four laser sintering materials, ten tribofilaments, and the new iglidur i3000 3D printing resin, igus offers suitable solutions for users across various industries.