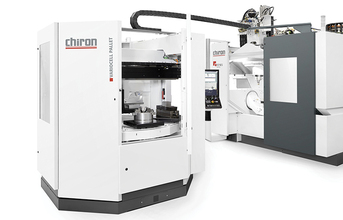
CHIRON Group is attending EMO in Hanonver from September 16 to September 21 with innovative must-sees relating to machining. Machining centers from CHIRON, STAMA and SCHERER, new automation solutions and an extended software program await visitors to the exhibition.
CHIRON: new variants of the 16 series and world premier of DZ 25 P five axis: At EMO, CHIRON is combining the new FZ 16 S five axis with VariocellPallet pallet automation for the first time. The new automation solution is aimed at machining small batch sizes and complex workpieces autonomously. Furthermore, the new DZ 16 W five axis will be presented live in action in Hanover. The highly-productive 5-axis double spindle machining center has already convinced those visiting the CHIRON OPEN HOUSE because of its unique combination of dynamics and precision.
The CHIRON DZ 25 P five axis is celebrating its world premier at EMO, designed for productive machining of large components in the automotive industry and aviation. With the 25 series, CHIRON is achieving a combination of productivity, precision and flexibility that has never been seen in this class before. With a spindle distance of 800 millimeters, the DZ 25 P five axis is predestined for double-spindle machining of aluminum structural components. It is operated and loaded on separate sides, which allows ideal access to the work area and a good insight into the process. The machine only requires a small amount of floor space thanks to its compact design. Furthermore, its optimal dynamics make it a compelling offering in this competitive environment. Visitors can experience the DZ 25 P five axis live in a new light in CHIRON's interactive showroom.
STAMA MT - trend-setting in complete machining for complex workpieces that are difficult to machine: Whether from the bar or the chuck, STAMA keeps setting new milestones in complete machining with the MT 7 and MT 8 systems' milling and turning machines offering innovative machining solutions. Since September 2018, STAMA has been offering new machining centers for 6-side milling and turning in one setup in the form of the MT 733 series, especially for complex components and materials that are difficult to machine. The MT 733 one plus will enjoy its world premier in Hannover. Like all models of the MT 733 series, it has a gantry design: this allows the machining process to gain a significant amount of stability on a thermal, mechanical and static level. The Galaxie® drive system in the B-axis bolsters this effect with its extreme power density, stiffness and positioning precision. The final result is highly dynamic and highly precise milling/turning and drilling operations, simultaneous 5-axis machining and integrated automation. These are the best conditions for a successful "first part good part" strategy. The MT 838 TWIN, presented by STAMA, is a HSK-A100 milling and turning machining center that is unique in double-spindle milling and turning of chuck components with a spindle distance of 600 mm.
Vertical turning from SCHERER for the customer's needs: Highly productive turning takes center stage again at SCHERER. The company is demonstrating its expertise with the VDZ 320 multi-functional vertical pickup turning machining center. The series can be precisely tailored to the customer's requirements thanks to numerous equipment options and variants. Options include another milling spindle and special modules for ball turning, bearing track milling and hobbing. An additional Y-axis in the main spindle ensures high productivity during complex machining.
CMS presents automation solutions that can be retrofitted: Automation is at the heart of retrofit specialist CMS's work as well. In Hanover, the company is showing how an out-dated machining center can be enhanced by a modern automation solution and how this can significantly improve productivity. Automation is gaining significant importance across different industries. That's why retrofits are an attractive and cost-efficient way for many customers to remain future-proof.
SmartLine software portfolio extended: This year, the CHIRON Group is extending its SmartLine program with ConditionLine and ProtectLine. The software modules can be implemented individually or together. They support the user in taking even better advantage of the machining centers' capabilities.
ConditionLine allows precise planning of maintenance work and repairs. The software is reliable at detecting abnormal operating behavior and wear in a timely manner. ProtectLine has a preventative function in protecting physical machining centers from collisions with help from a digital twin. The virtual machining center always runs ahead of the real one and shuts it down in good time if there are any collision risks.
Source: Chiron Group