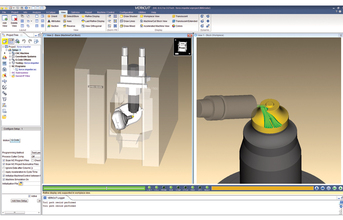
Removing the fear of multi-axis machining
CGTech, the developer of VERICUT software, has encouraged its customers to push the software to its limits. This can be well described using an example involving a creative NC programmer for a large aerospace engine manufacturer. They were looking for a faster way to make the leading edge of a titanium fan blade, and the NC programmer theorized that a new machining method could make the difference they needed.
Traditionally the process for making the part took many hours using a grinding technique. The NC programmer believed the part could be created using a 5-axis mill, but he knew he would need to convince his management before tying up the expensive machine for many hours cutting a test part. By using VERICUT to simulate the process, the programmer was able to create a video/review file to prove the process would work.
According to the Association for Manufacturing Technology, 5-axis mills and mill/turn machines have increasingly become popular, for a good reason. They enable the manufacturer to drastically reduce machining time and the number of set-ups required to complete a job. Simulation software takes the fear out of programming a multi-axis machine. When an NC program can be simulated, from the same code that will be sent to the machine, there is no excuse for not taking full advantage of a 5-axis machine's capabilities.
Machining before machine arrival
Even today, with ups and downs in machine tool sales, there is still considerable time between the date when the machine is ordered, and the date that it is installed and ready to cut the parts. With simulation software, the manufacturer can be ready to create parts on the first day the machine is installed.
CGTech has partnerships with many of the leading machine tool companies and they will often supply the CAD geometry for its joint customer's machines - before the machine is even shipped. The manufacturer can then be proving out programs right away. Some of the customers can discover the efficiency and suitability of the machine configuration ordered even before the machine is delivered. By catching the machine specification mistake early, the customer can change the order before the machine is delivered.
(Continued on next page)