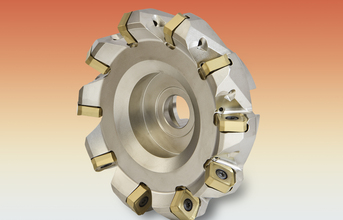
The patented cutting edge geometry enables a smooth cutting action and good surface quality when roughing. For the machining of large parts such as steel components or motor blocks, an efficient milling system is required. As time saving is extremely significant when machining blank surfaces, the increased depth of cut represents an advantage for operators. Simultaneously the power consumption should be kept as low as possible. The new milling cutter absolutely fulfils these requirements reaching depths of cut up to 8.4 mm on steel, stainless steel and cast iron.
When developing the new milling cutter the Ceratizit R&D department put particular emphasis on the cutting geometry. "Applying a special technology we have produced double positive rake faces thanks to which the tool cuts particularly smoothly," explains Mario Wolf, Product Manager at Ceratizit. For the operator this means that MaxiMill 271-17 consumes around 20 percent less power compared to conventional milling cutters while being able to obtain notably larger depths of cut. In addition, customers are able to benefit from this economically attractive tooling solution as the insert is provided with eight usable cutting edges.
Process security and optimum wear resistance
Ceratizit considers it important that the milling processes are both stable and secure. Mario Wolf says: "We built extra-large chip pockets in the MaxiMill 271-17 which optimally evacuate the swarf. At the same time we have managed to keep the cutter body stable and compact." Another advantage is that vibration is reduced to a minimum, which ensures the excellent stability of the milling process.
Furthermore, when designing the geometry of the insert it was an important goal that the cutting edges are inclined downwards which enables a peeling cut. The cutting forces and thus also the heat are evenly distributed. "Thanks to the combination of maximum cutting parameters and the selected HyperCoat carbide grades, optimum wear resistance and maximum tool life of the inserts is guaranteed," explains Wolf.
MaxiMill 271-17 shows excellent results in the field of mechanical engineering, automotive industry and medium heavy-duty machining, but is as well extremely successful when applied in machining operations of the ship building sector and the oil industry. There the components applied consist of nickel-based alloys which are both tough and abrasive, a challenge easily met by MaxiMill 271-17 thanks to the positive cutting action.
Flexible application
This Ceratizit tooling solution is available with various chip grooves. Geometry -F is characterized by a smooth cutting action which is why customers normally use it for finish machining or for the machining of stainless steel.
Geometry -M is suitable for universal application and represents the first choice for steel as it provides an optimum combination of smooth cut and stability.
For severely interrupted cuts and generally difficult machining conditions geometry -R with its robust and very stable cutting edge is the best choice.
END