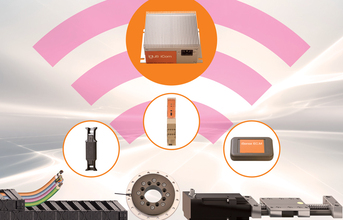
‘Machine Learning', ‘Big Data' and ‘Industry 4.0' - the real potential customer benefits from digitisation are often hidden behind these buzzwords. Intelligent products such as igus smart plastics, for example, enable companies to increase the reliability of their systems, plan maintenance tasks accurately and thus save costs. The way this works is demonstrated by igus with new ideas at the Hannover Messe 2018.
igus has been developing a family of products since 2016 under the heading 'isense', where various sensors and monitoring modules add intelligence to plastic solutions such as energy chains, cables, linear guides and slewing ring bearings. They measure among other things the wear during the operation and alert the user early enough to plan repair or replacement. By networking using the igus communication module (icom), the online status and alert display, for example via a PC, tablet or smartphone, is just as possible as a direct integration into the customer's infrastructure. These smart plastics are already predicting the service life of numerous customer applications, such as in the automotive industry. They are continuously developed in close cooperation with customers. These novelties were presented by igus at the Hannover Messe.
Individual integration of smart plastics The improved isense modules, which use sensors to collect data from the energy chain, cable, linear guide or slewing ring bearing, are equipped with a serial interface and can be easily integrated into a control cabinet. A data logger allows the storing of values on an SD card. The data measured by the different isense systems are then sent wirelessly to the icom module, summarised and processed. The customer has the choice of various concepts for integration into their own infrastructure.
In this way there is an option for the icom to send the data from the sensors to a PC or integrate the data via the computer into the existing software environment and intranet solution. In addition, a connection to the igus Data Center is possible. In this case, the maintenance recommendations via Machine Learning and AI algorithms are constantly compared and defined with the experiences of many existing applications, for example in the large igus test laboratory spread over a floor area of 2,750 square metres. "Due to the numerous test findings that are fed into the online service life calculators, we are able to predict precisely how long an e-chain will work reliably in a particular application," adds Richard Habering, head of the newly established smart plastics business unit at igus. "The isense components provide the customer with additional safety through a permanent service life update. This is because it includes the current ambient conditions of the actual application. Maintenance and replacement occurs only when it is really essential. This saves time and maintenance costs."
END