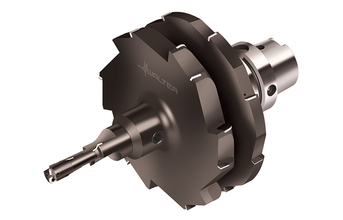
Machining chassis components is not easy, as the process usually involves difficult-to-cut materials. Many chassis components also have a long, slim shape, which makes them even more difficult to machine. Walter AG, based in Tübingen, is a sought-after solution partner in this field. The company tackles these specialised challenges with efficient tool geometries and a range of ingenious hybrid tools unrivalled on the market.
Drag bearings for the front wheels of a car are 50 cm long or longer. They are usually made from materials with difficult cutting properties. Aluminium is generally used for cars, whereas commercial vehicle chassis components are generally produced from cast iron and their dimensions are even larger.
The length and often demanding shape of the work pieces makes machining these drag bearings and other chassis components a difficult exercise. Especially since the finished parts - whether
bearings, suspension arms, longitudinal swinging arms or subframes - will have to withstand exceptionally high loads: They will have to support the steering motion, compress and decompress, ensure a secure connection to the vehicle body and do their job perfectly even in the worst road conditions (to mention just a few of the demands placed on them).
Robust materials
The materials used to manufacture chassis components are suitably robust - and consequentiality difficult to machine. For example, the aluminium alloys, which predominate in the car sector, can produce chips that are often between 10 and 50 cm long. Removing these chips smoothly and cleanly is barely achievable.
The challenges begin much earlier, however at the clamping stage and in the spatial configuration of the machining situation. The work piece must be securely clamped and accessible for machining from all required sides. The tool must be long enough to do its job between the clamp and the component optimally. The time-honoured rule applies to clamping and tools here: As long as necessary but as short as possible. The most important thing is to get a handle on the cutting forces. The length of the pieces being machined and the tools may cause such substantial swinging movements during machining that clean and precise machining is no longer possible.
"This can be entirely or at least substantially prevented with a tool geometry specially developed for this purpose," explains Roland Hanischdörfer, PCD Special Tools Product Manager at Walter AG: "Our tools are specially designed for machining chassis components."
There are essentially two effects generated by using the correct microgeometry, which counter the undesirable swinging movements: Either the stability of the tool limits the swinging movements to a minimum or eliminates them, or the forces generated during machining cancel each other out. Which effect is produced, or whether a combination of both is employed, depends on the actual machining situation. "Our tools are able to do either," says Roland Hanischdörfer.
Hybrid tools improve efficiency
This is not enough for the specialists at Walter, after all, their customers in the automotive sector are subject to constant competitive pressure and consequently pressure to optimise. The Tübingen-based company has therefore developed a wide range of tools to facilitate efficient machining of chassis components: Hybrid tools combining solid carbide indexable inserts with polycrystalline diamond inserts (PCD).
(Continued on next page)