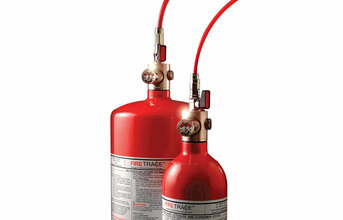
Investing in an industrial CNC milling, turning or grinding center is a smart business choice. A CNC machine can produce parts with amazing speed, accuracy and consistency, which can give you the competitive edge you need to thrive in a tough economy. However, while CNC machines are designed to be as safe as possible, they can be susceptible to fire.
Many CNC/EDM machines operate using oil-based metalworking fluids, coolants and lubricants. These oils and fluids are flammable, with flash points ranging from 170-350° Celsius, and are continually exposed to extremely high levels of friction and heat. A mistake in programming or a mechanical failure can quickly turn a normal machining operation into a hazardous situation. Even a single spark can turn the ready supply of coolant oil and vapour into a major fire in seconds.
The result:
• Lost productivity/ Downtime
• Lost customers
• Lost profits & market share
• Loss of life
• Property Damage and recovery cost
Advantages/ disadvantages of oil-based fluids
Straight oil-based metalworking fluids, coolants and lubricants offer several advantages over watersoluble fluids. The use of oil-based
metalworking fluids in industrial CNC and EDM machines will increase tool life, reduce friction and heat, improve surface finish and help flush dross from the work area. Perhaps the greatest advantage of straight oils is the excellent lubricity or ‘cushioning' effect they provide between the cutting tool and workpiece. This is particularly desirable for applications that require high quality surface finishing.
The greatest disadvantage of straight oils is their poor heat dissipating properties, which leads to an increased fire risk, which is why they are usually limited to low temperature and low-speed operations.
(Continued on next page)