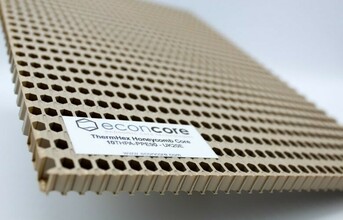
EconCore, a global leader in honeycomb technologies, has developed new honeycomb cores for laminated sandwich panels made with SABIC's NORYL GTX™ resin, a polyphenylene ether (PPE) blend, and EconCore's proprietary technology. The new honeycomb core presents higher heat performance, better dimensional stability and lower water absorption compared to honeycomb structures made with traditional thermoplastics. These properties enable the new core material to be used in demanding applications such as certain automotive, e-mobility and photovoltaic components. Furthermore, combining this new honeycomb core with thermoplastic composite skins to produce an all-thermoplastic sandwich panel can facilitate recycling. These desirable performance attributes and enhanced sustainability can open new market and application opportunities for EconCore honeycombs made with NORYL GTX resin.
"We turned to SABIC for expert assistance in enhancing our honeycomb cores with high-performance thermoplastics to expand our product's use in a range of applications and overcome the limitations of incumbent materials," said Tomasz Czarnecki, chief operations officer, EconCore. "Our many years of collaboration with SABIC and the company's broad materials portfolio gave us high confidence in the success of this initiative. We have been very impressed with NORYL GTX resin's ease of use in conversion and appreciated the fact that it works well in our existing equipment. We believe its well-balanced properties will allow honeycomb cores to be used more widely in transportation, clean energy and e-mobility applications."
Benefits of Honeycomb Structures
Thermoplastic honeycomb structures deliver a high performance-to-weight ratio and efficient energy absorption under impact. The rigidity of honeycomb sandwich panels is known to exceed that of monolithic materials, including solid composites. Also, sandwich structures are an effective means of reducing mass in a wide range of weight-sensitive applications. Combined with an effective, in-line integrated sandwich panel production technology, this weight reduction has positive implications for overall production cost savings and environmental responsibility.
In addition to reducing raw material use, the honeycombs support recyclability. Combining the PPE-based core structures with thermoplastic composites skins, such as those based on nylon, can result in a recyclable and sustainable solution.
Furthermore, sandwich panels made exclusively with thermoplastics can be efficiently processed into finished parts with complex geometries using compression molding processes, which can help reduce cycle times.
High-heat Performance
According to EconCore, its new honeycomb structures deliver higher heat performance, greater dimensional stability and lower water absorption than alternative materials such as nylon. Due to this high performance, the cores may also demonstrate good compatibility with thermoset composite skins. Because the honeycomb exhibits high load-bearing capacity even at temperatures up to 180°C, it may be a good candidate for lamination with thermoset prepregs in processing environments where high curing temperatures are typically applied. The honeycomb can also potentially be used for applications where sandwich panels must deliver high performance at elevated temperatures.
Unique Conversion Process
EconCore honeycombs are produced from a single continuous thermoplastic sheet using the company's patented technology. In this unique process, the material is extruded and in-line formed into the honeycomb structure without the need for secondary operations. Specifically, this involves a sequence of extrusion and thermoforming steps to transform the extruded film into a half-hexagonal web that is directly folded into a thermoplastic honeycomb structure.
The high efficiency of this continuous process minimizes production costs, making the product very competitive economically. Furthermore, the technology allows for integration of the skin lamination step in-line with the honeycomb core production, providing opportunities for effective, continuous manufacturing of value-added laminated sandwich panels.
EconCore's technology also offers expanded freedom to design and produce a wide range of honeycomb cell sizes, core thicknesses and densities. The company has licensed its integrated technology for production of lightweight honeycomb panels in specific configurations to several leaders in the industrial packaging, automotive, transportation and building and construction industries.
High-performance Resin
SABIC's NORYL GTX resin provides high heat resistance during processing of up to 240°C (465°F), with conductive grades that may be used in powder-coated automotive body panels. Compared to nylon, NORYL GTX resin has lower water absorption and a lower density, reducing part weight. This material offers excellent impact performance and stiffness across a wide temperature range. SABIC is also currently developing a new grade with extreme low-temperature impact performance for potential use in honeycomb cores for electric vehicle (EV) battery protection.
"Our most recent collaboration with EconCore underscores our strategy of giving customers across different industries access to higher-performance thermoplastic solutions that can address the stringent requirements of their most demanding applications," said Tjerk Lenstra, senior business manager, NORYL™ Portfolio, SABIC's Specialties business.
"Our unique portfolio and deep product and application expertise, combined with EconCore's proprietary technology, open up new metal-replacement and weight-out opportunities in a wide range of important segments, such as e-mobility and photovoltaics," said Luc Govaerts, director, Formulation & Application Development, SABIC's Specialties business. "We look forward to continuing our work with EconCore to create new customer solutions using our specialty materials."