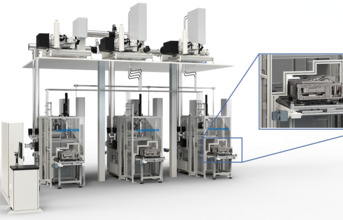
In the context of the White Goods/Home Appliances industry, Marposs' Dryer Heat Pump Leak Test application is a high-tech end-of-line test that ensures very high product quality without sacrificing the necessary high productivity to meet market demands at production sites. This solution utilises a hard vacuum helium leak detection system across the entire finished assembly, offering the most reliable method for detecting global leaks in circuits.
The testing method employs 100 per cent Helium as the tracer gas, with mass spectrometer measurement in a vacuum chamber, making it the most effective among various leak testing systems for detecting even the smallest leaks. Marposs' in-line leak test machines can detect leaks in heat pump assemblies down to a threshold range of 10-5 mbarl/s. For comparison, traditional nitrogen leak tests in water tanks typically yield results in the range of 10-2 mbarl/s (one bubble with a radius of 2 mm in 1 second), factoring in human guesswork and potential undetected leaks.
A significant challenge in automatic testing lies in the large manufacturing tolerances of coolant tubes. To address this, Marposs has developed a highly flexible coupling design that facilitates automatic connection of the inlet pipe, despite uncertainties in assembly positioning. The coupler has a large compensating capacity, even when a large distance is covered up and down to reach the connection point with vertical pneumatic movement.
What was once a manual test has been successfully automated, significantly benefiting production efficiency. The modular design, accommodating from one to several leak test stations, offers versatile productivity in fully automated settings.
Leak testing is crucial for all thermal exchange processes using refrigerant gases, ensuring the long-term tightness of refrigerant-containing components and performance efficiency in terms of heat exchange. Increasing demand for energy-efficient heat exchange systems underscores the importance of accurate HVAC product leak testing. As attention shifts towards refrigerant compounds' environmental impact, reliable leak testing solutions become indispensable.
To ensure accuracy and compliance with legal leakage thresholds for each chemical compound, comprehensive EOL leak testing is imperative for both components and final assemblies. Detecting leaks guarantees sustained thermal efficiency and performance over extended periods, essential for product longevity and consumer satisfaction.
Marposs solutions are strongly focusing on enhancing leak testing performance for more efficient products, utilising hard vacuum test chamber methods and additional functional tests to augment test station value. Basic tests like preliminary gross leak tests on the dryer heat pump assembly using air pressure decay techniques help identify major defects early, optimising production processes and data management.
Additional features include manual sniffing systems for maintenance and troubleshooting, and functional tests for electro-pneumatic devices within the unit, all integrated with full test traceability for warranty purposes. Marposs also offers a helium recovery system with high efficiency (85-95 per cent), recycling helium within a closed system to maintain test accuracy and reliability.
Helium purity is closely monitored, ensuring correct levels through refilling and final compression to required test pressures. The recovery output provides leak test set points to the HLT machines so that data outside the acceptable range generates alarms to avoid false leak detection. The fully integrated process gives better accuracy and reliability to the system, with the shortest return on investment as ever.