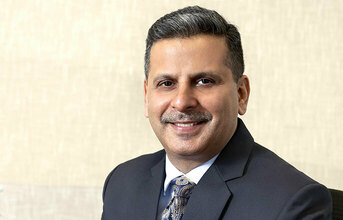
How has the Indian manufacturing sector transformed over the past year, and what key developments have contributed to this surge in hiring intentions?
Indian manufacturing sector is a key economic driver that accounts for 17 per cent of India's GDP. To strengthen India's position as a major centre of manufacturing, we aim to export goods worth $1 trillion by 2030. As per the various government initiatives, by 2025, manufacturing is expected to contribute 25 per cent to the economy.
As per the data from Quess Corp., the manufacturing sector has showcased 93 per cent quarter-on-quarter growth from FYQ2 2022 to FYQ2 2023. India has significant global market potential, thanks to elements like the expansion of electricity, stable employment, a young and educated population, and abundant raw materials. It is well-positioned to benefit from the value chain thanks to its raw material assets, industrial know-how, and entrepreneurial spirit. Prospects are further improved by options like contract manufacturing. Thanks to the Ministry of Micro, Small & Medium Industries, India has a thriving startup ecosystem that supports the growth of new micro and small businesses.
India's manufacturing ecosystem has seen several key developments in the recent year that have contributed to a surge in hiring intentions. The industry has showcased an increasing demand for senior professionals with 12+ years of experience, who continue to dominate. Manufacturing has been more export-oriented, which increases the requirement for organised staffing. Government schemes such as PLI, Make in India, Skill development and apprenticeship promotion and the EV boom has created job opportunities and contributed towards the expansion of manufacturing sector in India.
What skill sets and talents are in high demand given the manufacturing landscape's rapid evolution?
The emergence of Industry 4.0, integrating digital technologies, automation, and data analytics in the production processes, has led to a rapid evolution in the manufacturing landscape. Adapting to the evolving requirements and opportunities in the industry requires workers to possess both fundamental human skills and digital skills. Critical thinking, creativity, and people management are some of the fundamental human skills that are in high demand. The technical skills that are well-regarded in the field include CNC (Computer Numerical Control), welding, brazing, tool designing, and mechatronics. Technical, human, and digital skills together allow workers to come up with novel ideas, solve complex problems, and work well with others. According to a World Economic Forum study, these are among the top 10 skills for the upcoming ten years.
The modern manufacturing workforce increasingly requires these skills, in addition to digital competence. Companies are actively looking for workers who not only have digital skills but also excel at humanmachine interaction and have a basic understanding of information technology. This combination of digital and human skills is seen as essential to work alongside automation effectively. To acquire these skill sets and talents, workers need to engage in reskilling and upskilling programs that can help them update their knowledge and abilities. Reskilling courses are a must for excellence and performance and upskilling courses ensure that employees are ready for the next level of growth, which also helps in motivating and retaining the existing workforce. These programs can be offered by employers, educational institutions, or online platforms. This will ultimately increase employability, productivity, and career advancement for workers, as well as improve competitiveness, innovation, and sustainability for employers.
How is the manufacturing sector addressing diversity and inclusion in its hiring practices?
We have noticed a significant, multifold increase in terms of incorporating Diversity and Inclusion (D&I) initiatives in the hiring practices. The manufacturing industry hardly has a bias while hiring employees. Employers are open to hiring people from diverse backgrounds for their exclusive lines and factories. Female employees are preferred to work at shop floors, thereby creating more job opportunities and breaking biases pertaining to gender.
A few industries such as electronics have started to prefer employing women owing to the nature of work that needs handling of minute components and requires soft-handed employees. Even larger OEMs have shown progress in terms of incorporating female and physically challenged workforces. Despite the wide acceptance, there are some industries such as foundries which inadvertently prefer a particular gender, as the nature of work involves heavy lifting activities. A diverse workforce has shown greater productivity in manufacturing and industrial and has resulted in higher retention of workers.
Continue Reading on Page 2