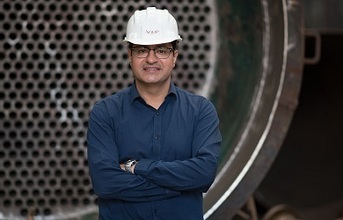
Anup Engineering was started in the year 1962, briefly tell us about its evolution into a major player in heavy fabrication industry since then.
The Company originally started as a manufacturer of dishends/pipe caps (components of a pressure vessel) to cater to a growing textile / chemical industry in Ahmedabad. In the 1970s, Anup started manufacturing centrifuges and also emerged as a capable supplier of aerospace components to ISRO. Subsequently graduated to become a manufacturer of centrifuges and pressure vessels / heat exchangers over the next three decades.
By the turn of the century major investments in core sectors like refineries / petrochemicals / chemicals started happening in India as well as in middle east and the USA. This created significant demand for process equipment and hence more opportunities for process equipment manufacturers like Anup. By the year 2010 Anup was an established player for supplying mid-end process equipment with a reasonably good infrastructure. It was after 2011 that Anup rapidly grew to become a fabricator of choice for some of the most challenging business segments viz shutdown / replacement markets, solely because of its exceptional performance in terms of on time delivery and quality.
How would you analyse the overall engineering business in India and where would you place Anup in terms of its capabilities and project delivery records?
Engineering business in India is expected to continue its growth trajectory because of its huge engineering talent pool, abundant and highly skilled workforce, large population with spiraling consumption and growing energy needs. Anup Engineering has excelled in the last six years to generate an exceptional on time delivery record apart from excellent product quality and customer focus. If we specifically look at the shell and tube exchangers in the whole gamut of process equipment, Anup is currently a market leader from all perspectives - be it the volumes or versatility in terms of sizes, metallurgies or applications.
Over the years, Anup Engineering has developed the skill and technology required to carry out highly critical and specialised jobs, which also involves working with unconventional materials. Tell us about this. How did you develop this capability?
Whenever our customers visit our facilities there is one quality which they admire unfailingly and that is our versatility. Perhaps Anup Engineering would be one of those rare companies having the entire range of metal processing capabilities under one roof - forming, bending, cutting, machining, welding, coating/surface treatment and heat treatment. These facilities are helmed by experts with a lot of experience in each of these aspects. Couple this with our design capabilities which set us apart from other manufacturers - thermal, finite element analysis, fatigue analysis etc. These skills and capabilities impart us the ability to assess key aspects of any material / design combination and this accurate assessment is the reason behind our confidence to take up extremely challenging orders.
Continuing from the above question, has it been challenging for you to acquire the technology and machinery required for such a different segment? Are these easily available in India or did you have to import some?
It's the same set of machines which are used to cater to process equipment fabrication for different industry sectors. As such the most critical machineries have been imported - primarily from West Europe which was traditionally strong in the heavy engineering business until 2005. However, quite a few of these machines are now indigenously available.
(Continued on the next page)