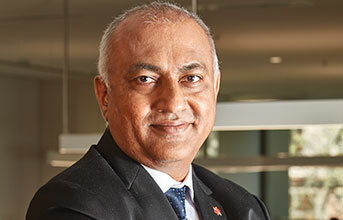
Could you please provide an overview of the new offerings your company has recently introduced, with a particular focus on two- and four-wheelers, including air filtration systems, snorkels, and various blow-moulded products?
Lumax Cornaglia's (a 50:50 joint venture between Lumax Auto Technologies Limited and the Cornaglia Group of Turin, Italy) facilities based in Chakan, Pune, and Pantnagar, Uttarakhand, specialise in automotive air intake systems. Initially, we began as an air filtration and air intake systems company, providing ducts and vehicle filtration solutions to OEMs. However, over the last four years, we have expanded into tank manufacturing. We now specialise in manufacturing AdBlue Tanks (Urea Tanks) that comply with the BS6 regime and are adept at managing nitrogen content and nitrogen dioxide (NO2) levels.
Additionally, we have diversified into rotational moulding technology for plastic fuel tanks for commercial vehicles at our new plant located in Chakan, Pune. Initially, these plastic fuel tanks will be integrated into commercial SOPs this year, with plans to expand to other OEMs. Thus, our Chakan Facility is a one-stop solution shop for all moulding technologies, including advanced plastic polymers such as injection moulding, blow moulding, 3D moulding, and rotational moulding, catering to current automotive OEM requirements.
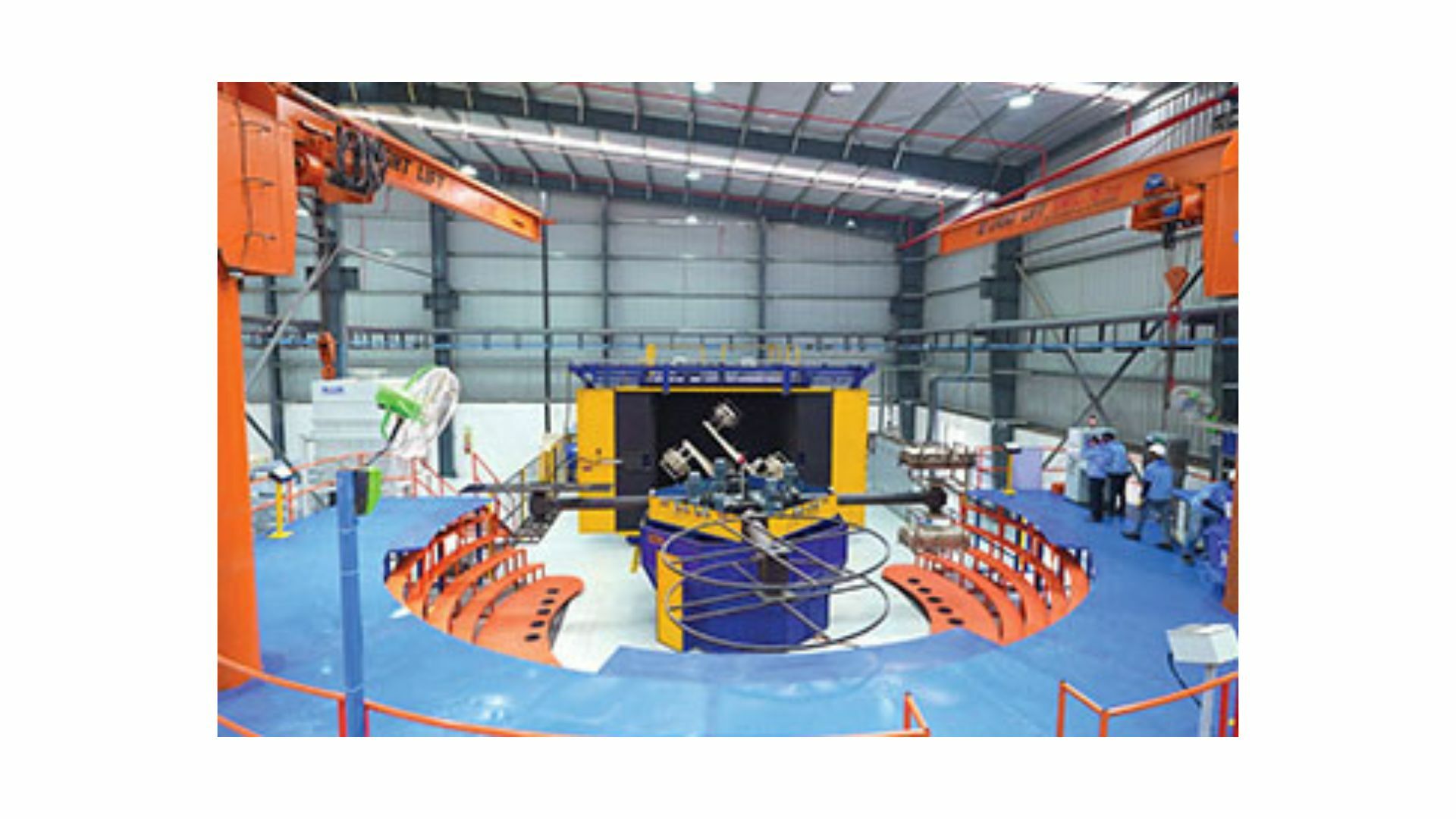
What were the driving factors behind the development of these new products, and how do they address the evolving needs of the automotive market in India?
The primary driving factor was identifying commercial business opportunities within the regulation-driven regime, as regulations like BS6, EURO 6, and Corporate Average Fuel Economy II (CAFÉ II) continue to evolve and be implemented in the market. We recognised that in the advanced plastics segment, our joint venture partner, Cornaglia, possessed some exceptional and mature technologies developed in Europe, the US, and other markets. We foresee the implementation of stricter emission norms in the future. So, before the eventual shift of more than 80 or 100 per cent towards EVs, hybrids, or alternative fuels happens, there remains a significant need in the Indian vehicle industry for advanced product solutions. Our current offerings aim to address this need effectively.
Could you elaborate on the materials used in these air intake systems?
We have used various advanced plastics such as TEEE, specialised versions of polyolefins, special grades of polyamides, polyurethane etc.
How do you anticipate rotational moulding's impact on the market, considering you have recently introduced it?
Rotational moulding offers adaptability to smaller volume products, providing cost advantages and manufacturing efficiency. While our initial focus is on plastic fuel tanks for commercial vehicles, we anticipate its broader applications on the roofs of vehicles like three-wheelers, e-three-wheelers, and cabinspecific exterior moulding requirements from various agricultural and off-highway vehicles. The potential of rotational moulding extends beyond automotive and holds immense opportunities in non-automotive sectors where we currently do not have a presence.
Could you highlight the key features and benefits of each of these new offerings, particularly in terms of performance, durability, light weighting and environmental impact?
Advanced plastics contribute to the light weighting, corrosion resistance, recyclability, and efficient packaging of vehicles due to their inherent properties. They offer anti-corrosive capabilities, crucial for hydrogen waste and alternative fuel management. Additionally, our products adapt well to vehicle packaging and are space efficient. We are also developing our in-cabin filtration systems and aggressively working on thermal management systems, where we intend to introduce de-gassing tanks or de-gas bottles, particularly in the EV space, through our joint venture, Lumax Cornaglia. We hope to expand further on this portfolio.
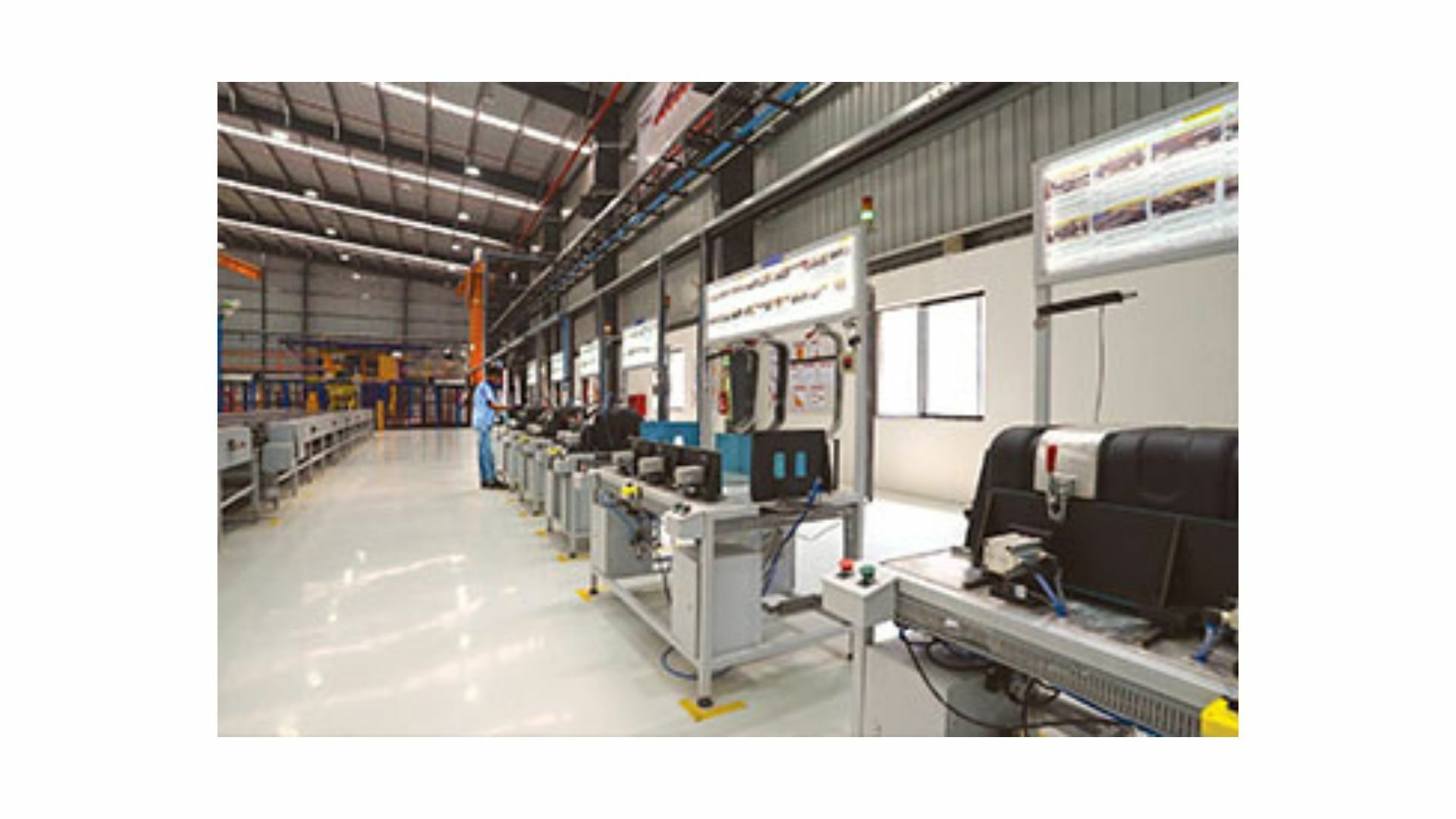
How do you anticipate these new offerings will impact your company's market position and competitiveness within the automotive component industry?
Through our joint venture, Lumax Cornaglia, we aim to be recognised as leaders in light-weighting and energy-efficient auto component manufacturing. Even on the ICE powertrain, our filtration and air intake systems contribute to lower emissions, aligning with evolving industry needs. Going ahead, we are ready to adapt our powertrain on basis of evolving industry demands.
What are your plans for further innovation and expansion of your product line, through Lumax Cornaglia JV?
We will continue aggressive testing in thermal management for powertrains and aim to contribute to regulatory compliance. Currently, plastic fuel tanks are compliant with the existing norms. Lightweight materials are becoming mandatory for all Original Equipment Manufacturers (OEMs), and our products are well-suited to play a significant role in meeting this requirement.
With the rise of electric vehicles, how is your company preparing for the evolving automotive emission systems?
We are heavily investing in thermal management solutions through our joint ventures, including Lumax Cornaglia, to mitigate emissions and manage heat efficiently. We are hopeful that one of the major OEMs will have a non-electric vehicle with this product available for SOP next year. Going forward, there will be other opportunities available.
How does your company approach research and development to stay ahead in automotive component technology?
Research and development are crucial. We aim to maximise the benefits offered by the government's PLI scheme. Lumax Auto Technologies is fortunate to be an approved player under the PLI scheme. One of our products from this joint venture, the Urea Tank, falls under the scheme.
Additionally, we have a strong research and development facility in Chakan (Pune) with a team of engineers ably supported by the Cornaglia Global R&D team.
At present, we are meeting the OEM requirements satisfactorily. However, with the emergence of new vehicle platforms, we need to invest heavily in research and development. We estimate that this investment may account for more than five per cent of the joint venture's revenue and will be utilised for R&D to meet industry demands.
How does your company address skill development for the largely untapped workforce?
We aim to foster an Operating Engineering culture and plan to initiate campus recruitment drives. Our assembly stations, with automated operations, offer opportunities for diverse hiring. However, soon we would be kickstarting our campus recruitment programs and over the next 2-3 years, we aim for over 50 per cent diversity in our joint venture.
What is your vision for the future of your company in the automotive industry? Highlight key areas you would be targeting for growth?
We aspire to be among the top two players in every product segment through our joint ventures. Out of eleven, four of our joint ventures are in that space. However, in the next five to ten years, we hope to have all of them in the top two-player space. In addition to providing critical mass, this will give access to international technologies to serve the expanding Indian market, which is currently the world's third largest market for auto components.