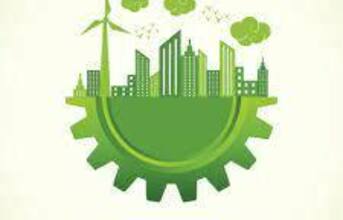
The late UN Secretary-General, Kofi Annan, said, "Our greatest challenge in this new century is to take an idea that seems abstract - sustainable development - and turn it into a reality for all of the world's people." One of the keys to meeting this challenge is digitalisation. Digital transformation is a journey of continuum towards the self-optimising plant, which capitalises on data to generate knowledge. Industrial AI provides companies with massive learning ability and can be a strategic business advantage, combining the power of analytics and AI machine learning, with crucial guardrails of domain expertise, to accelerate return on investments (ROI) from industrial data.
Willie K Chan, CTO, AspenTech, highlights the crux of the situation, "Domain expertise is the secret sauce that separates industrial AI from more generic AI approaches. Industrial AI will guide innovation and efficiency improvements in capital-intensive industries for years to come." Industrial AI enables general engineers to leverage machine learning without being advanced data specialists or specialist engineers. AI algorithms only represent five per cent of the software source code with the remaining 95% derived from domain expertise.
Driving Value Via Digital Twins
A digital twin is a virtual model of a physical plant. It provides a valuable model of the physical asset, its behaviour and performance so plant knowledge workers can safely explore what-if scenarios without putting people or the asset at risk. It provides a valuable model for assessing asset health, forecasting, and recommending action to avoid degradation and asset failure events. Perhaps most important, it creates a business model representing scenarios for product creation, operations, sustainability, effective asset utilisation, risk, customer satisfaction and profit.
The digital twin is an evolving digital profile of the historical, current and future behaviour of a physical object or process that helps optimise business performance. It is based on models and real-time data across multiple dimensions, including business performance, asset planning, the physical asset, equipment condition and reliability, chemical process performance, safety and risk, energy, and sustainability, operating and project timespans and more.
The digital twin creates an evolving profile of the object or process that provides insights on system performance, guiding actions in the physical world - such as changes in operating strategies, regulations and business objectives, safety and maintenance. The digital twin may be updated in real-time or periodically, taking advantage of asset data to stay up-to-date, and increasingly made intelligent by AI agents.
Reducing Energy Usage By 2030
The Federation of Indian Petroleum Industry (FIPI) recently named Aspen Technology its 2021 Digital Technology Provider of the Year award. Anchoring this award was a landmark Bharat Petroleum Corporation Limited (BPCL) customer case study that showcased how the Mumbai Refinery adopted a real-time digital twin, based on the use of AspenTech's digital twin and Advanced Process Control (APC) products. The digital twin has been implemented online and integrated with an associated advanced process control (APC) solution, such that the optimisation engineer uses the digital twin on an hourly basis to inform the adjusting of the APC levers for optimum steam use efficiency and amine utilisation effectiveness.
Contributing 15 per cent to India's refining capacity and ranked 44th position in Platts Top 250 Global Energy, BPCL Mumbai Refinery aims to reduce energy usage by 37 per cent in 2030. BPCL has achieved significant energy reductions, with the use of an online digital twin, integrated with APC software in one of the most significant steam usage areas in the refinery, namely, the amine stripping and regeneration process.
Essentially, BPCL had deployed Aspen DMC3™ software with a digital twinning approach - to achieve about $1 million savings in utilities annually. The company is the first amongst Indian PSU refineries to implement APC in Amine Regeneration Units (ARU) and integrate digital twin output to APC. With an estimated payback of fewer than six months, the company could effectively reduce energy usage in changing sulphur content in crude slate, which had originally resulted in sub-optimal amine regeneration. The Aspen DMC3 software enables the adoption of a scalable and sustainable approach via its patented adaptive process control technology.
In doing so, the intelligent plant can respond automatically, achieve real-time agility and maximise performance in a seamless yet, robust manner. With the ability to accelerate deployments, process manufacturers can achieve benefits faster, improve ROI and enhance overall performance.
A Sustainable Path Forward
Companies with the ability to balance profitability and sustainability can address the dual challenge more efficiently in the new industry normal. The dual challenge mandates the need to address increasing resources for a growing population with increasing standards of living while balancing the need to meet sustainability goals.
In a volatile marketplace, supply chain management is critical, as sustainability and resiliency are two sides of the same coin. FPCO, Japan's largest manufacturer of food containers and a logistics supplier, is one company that can achieve this critical balance. FPCO is committed to environmental advancement, avidly recycling used food containers and PET bottles. With more than a billion containers sold each month, selling recycled products needed to be an economically sustainable activity. The company chose aspenONE Supply Chain Management (SCM) to provide stable and responsive food distribution in an efficient, sustainable, as well as environmentally friendly manner.
Industrial AI can help companies navigate increasingly complex supply chain options and decisions. Momentum from rapidly changing global carbon mitigation necessitates focusing on energy transition across Asia, as cost and carbon footprint reduction come into focus on the agenda.
Digitalisation In The New Normal
Cost and carbon footprint reduction will remain high on the agenda. A shift in refining production mix towards chemical feedstocks is expected, as growth in chemicals is expected to account for about half of the near-term demand growth for oil in Asia. Mega integrated plant projects can address changing market demands efficiently and industry trajectory shifting from oil to gas consumption continues. Natural gas and renewables can address the increasing electricity demand, and the hydrogen economy is an emerging dimension.
As new energy areas gain momentum, rapid and powerful early concept design is crucial for the techno-economic analysis to ensure a profitable asset lifecycle. Hybrid models combining rigorous and AI-driven models are increasingly required to optimise complex operations, more accurately and autonomously. For capital projects, estimation and project progress transparency can unlock value. To manage project risk efficiently, it is necessary to visualise, analyse benchmarks and share data to increase speed and certainty. The result is a more agile, collaborative, and informed asset design - seamless with greater predictability in execution.