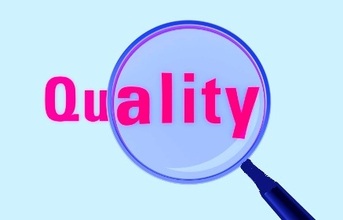
A crisis has a way of concentrating the mind. Conventionally, a lapse in quality could translate to massive recalls and even lawsuits. But despite their impact, these events are just a sliver of the full scope. If an organisation is to survive and remain ahead of its competitors and predators, it will need to build differentiation by providing specific value to their customer base. Creating and sustaining a competitive advantage is one way of achieving this goal i.e., the ability to possess some advantage relative to their competitors. And there exist several routes to achieving this - via building a cost advantage, which is fairly straightforward. A value advantage, where an organisation provides a differentiated offering perceived to be of superior value, or via developing a focus advantage i.e, focus on a specific market niche with a breakthrough tailored offering. The levers to accomplishing a sustainable competitive advantage are many; but if one were to delve deeper, you would find that quality forms the guiding thread across every internal touchpoint.
Indeed, it is important to keep the rare disaster from happening. But for organisations well focused on building a sustainable competitive advantage in the marketplace, simply reacting to quality problems is no longer tenable. For example - quality, cost, delivery (QCD) is a ‘three-dimensional' approach and if a problem exists with one dimension, the others will inevitably suffer. Being good at quality is therefore barely sufficient - they need to be smart about it as well. In effect, quality is no longer mainly a question of bottom-line savings but of top-line revenue generation.
Fundamentally, quality is about meeting or exceeding customer expectations: every day, every shipment, in each product, year after year. That's where the true value is, measured not only in higher revenues from greater customer satisfaction but also in higher operational efficiency and effectiveness due to increases in productivity and innovation—and even employee engagement.
For example - the ISO 9000's definition of quality is the ‘degree to which a set of inherent characteristics fulfils requirement'. The customer must be considered as well as the attributes of the product and the degree to which the product or service meets the needs of all stakeholders. Based on these characteristics we define the quality of a product as ‘good', ‘average', ‘excellent'. Adherence to a recognized quality standard is essential for dealing with certain customers or complying with legislation. If an organisation sells products in regulated markets, such as health care, food, or electrical goods, one must be able to comply with the health and safety compliance standards designed to protect consumer's interests.
Achieving these outcomes requires investment. And the secret sauce by which an organisation can build an intrinsic focus on quality and develop a sustainable competitive advantage in the market is via the adoption and implementation of TQM.
With origins tracing back to the 1920s, TQM has received the widespread acclaim that it currently enjoys, somewhere in the late 1900s. The credit for this revolutionary quality management principle goes to Edwards Deming, Joseph Juran, and Kaoru Ishikawa. Deming was hired by the Japanese industry leaders to come up with solutions that would improve industrial productivity, thereby increasing Japan's share in the global market. His statistical approach soon led to what is now known as the Japanese post-war economic miracle.
Later, Deming authored the 14 key principles of total quality management in his seminal work, ‘Out of the Crisis'. These principles defined the total quality management movement worldwide.
Total Quality Management (TQM) excellence helps organisations across the world increase market share and build the necessary sustainable advantage they need to succeed:
Enhanced Efficiency in Cost Management
Though the initial time and cost of installing an efficient Total Quality Management system is high, it has often been noted that this initial cost has long-term benefits. This preliminary expenditure ensures that undue expenses, wastages, and defects are significantly reduced. This helps enhance the overall cost management in the organisation.
Profitability on Investments
Efficient cost management contributes to higher productivity. There is also a marked increase in the economies of scale, which makes sure that businesses reap more at minimal costs. This productivity then accentuates the return on investment and the profitability of the organisation.
Employee Morale and Productivity
TQM involves the full commitment from the management. Once ingrained as a way of doing things, the business can reap the benefits of TQM - including a healthier bottom line. When your employees are more involved, it gives them room to be innovative and engaged, increasing their sense of job security and boosting their employee's morale.
Customer Centricity
Implementation of TQM measures results in superior quality service to customers. This enhances the customer's satisfaction and loyalty towards your products. Besides, businesses can go a step further and involve the customers in the overall process, creating a collaborative environment for all stakeholders.
Accentuated Adaptability
As there is a continuous evaluation at all the stages of the business, TQM ensures that the organisation can adapt to various changes in the economy. As a result, the organisation gets a higher competitive advantage and a strong image as a highly adaptable leader in the market.
So yes, organisations must learn to think about quality quite systematically and strategically. It is essential to build the early stage foundations of quality awareness namely, developing operating systems and promoting greater transparency about quality defects. The next stage of maturity focuses on strengthening cross-functional accountability and collaboration. At the third stage, quality forms the basis for much of the organisation's decision making, entwining itself so deeply that it becomes a part of the culture and essential to the company's value proposition.
Managing change and solving problems sounds quite simplistic. But in reality, this often results in disruption of colossal proportions if not managed efficiently. At the very core, organisations would greatly benefit from implementing the scientific method of problem-solving PDCA (Plan-Do-Check-Act), popularized by W. Edwards Deming. A simple four-stage effective approach for continually improving processes, products, and services. Problems are resolved using hypotheses and continuous feedback loops resulting in valuable learning and efficient, objective aligned outcomes.
Not every organisation needs to achieve the highest levels of quality maturity and certainly not all in one go. But every organisation must recognize that investments in quality capabilities open new opportunities for building sustainable competitive advantage.
END