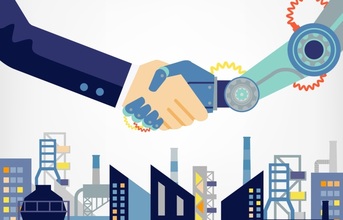
The rapidly changing global manufacturing landscape demands upskilling. The reason is simple: digital transformation has redefined the nature of work across major industries.
Future jobs will require an entirely new set of skills and competencies from the workforce. With over 600 million people below the age of 25 years, India has one of the youngest workforces in the world. This means that they need to be equipped with the right skills to help the country remain globally competitive. Skill development initiatives and reskilling programs are critical in creating the workplace of tomorrow.
Skilling in the manufacturing sector: With India poised to become a preferred destination for manufacturing, businesses need to realign their strategy to make skilling a key priority. The government has already initiated several programs such as ‘Make in India', ‘Skill India' and ‘Digital India' to leverage the potential of the country's large pool of workforce and accelerate economic growth. A skilled workforce will be able transform India into a global manufacturing hub in this decade. In recent years, India's aerospace manufacturing industry has witnessed global OEMs expanding their horizon to the country to globalise their supply chain in a cost optimized manner. The industry is currently booming and has leveraged global tendencies to deliver the best quality of products.
Need for skilling in aerospace manufacturing: Considering that aerospace manufacturing industry follows a ‘zero-error' policy, it demands a highly specialized skillset for these critical processes. Even though the industry is very aspirational, it is niche in terms of its approach and skills. There is a scarcity of quality aerospace centric education and vocation training in engineering colleges. This has increased the existing skill-gap extensively.
In light of this skill gap and lack of awareness, aerospace companies encourage talent with mechanical, electrical and electronic engineering education background suitable to upskill. The organisation provides them training and upskills them to meet the requirement. Similarly, ‘Training and Development' is another key focus area to enable existing employees to reskill themselves continuously and meet the dynamic job requirements. This reduces wastage of raw materials on the shopfloor while improving efficiency and speedy adoption of new technologies.
Learning with Aequs: As one of the global leaders of precision engineering and manufacturing for the aerospace industry, Aequs realised the need to bridge this skill gap and to nurture skilled talent to make India the manufacturing hub for aerospace industry. The company introduced Aerospace Knowledge Center (AKC) to provide a 30-month long program to fresh engineering graduates and diploma holders.
The primary objective of AKC is to bridge the knowledge gap by helping new recruits understand industry norms, applications and enhance their performance. The course is split into three levels. The level 1 comprises of basic training and qualified candidates move to level 2 for advanced training. Once both these levels are completed, they move to Level 3 to receive function-based training. Through such systematic training, companies can prepare the workforce to receive optimal productivity and quality. AKC has successfully trained over 620 candidates till date.
Besides this, Aerospace Knowledge Center has also been partnering with engineering colleges and technical universities to include aerospace manufacturing as part of their curriculum.
Skill development programs allow an organisation to remain agile and prepare for future disruptions while staying ahead of the curve.
END