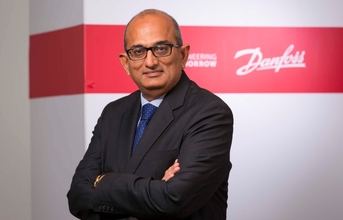
Can you please tell us about the implementation of Industry 4.0/Smart Factory in manufacturing facilities?
Digitization across industries has given rise to the phenomenon of smart manufacturing, paving the way to industry 4.0 that allows for the creation of flexible business models. In our opinion, this has contributed to reducing wastage of resources and the consumption of energy, promoting increased efficiency, faster turnaround, better quality, faster time-to-market, integrated supply chain and better security.
Earlier this year, Danfoss' compressor factory in Wuging, China was recognised among the 16 of the world's most advanced smart factories - as one of the so-called Fourth Industrial Revolution production sites. With its investment in smart technologies across the campus, the employee productivity has gone up by 30 percent, scrap costs down by 20 percent, and customer complaints by 57 percent.
By investing in smart technologies, companies are now able to produce customer-centric solutions which should ideally be the main architecture of our design principles. Industries should also look at incorporating design thinking in their products to ensure that we build them in a manner that helps our customers connect to various devices and gain maximum value from the products and solutions.
In simple terms, it also enables manufacturing facilities in achieving operational excellence. With emerging and advanced technologies like Internet of Things, 3D printing, big data & analytics, players like us are empowered to design, modify and create products & solutions that customers are looking for, thereby helping companies explore new revenue opportunities.
How does the technology make sense in Indian context where labour is available in abundance?
Productivity & Quality will increase with more smart manufacturing techniques. With right kind of skillsets being imparted to the new workforce, technology and labour can complement each other in tomorrow's production facilities, thereby leading to India becoming the manufacturing hub for the world.
Let us take the example of OLA or UBER where technology has improved customer experience but has also used the available labour force in an efficient manner.
We can see how the government is making use of smart technologies through policies like the eNAM market.
The most integral role of technology is towards aiding the process of productivity and efficiency of the labour workforce, and not to replace it.
In a market like India, the government's vision towards ‘Make in India' and the favourable demographic dividend makes it an attractive phenomenon for global manufacturers to set base in the country. Furthermore, it also makes the process of up-skilling an uncomplicated process and they are more receptive towards the innovation and usage of newer technology.
By enhancing our skillset and adopting ‘smart manufacturing', India can surely be positioned as one of the top three manufacturing destinations by 2020.
Technology upgradation calls for disruption as well. What disruption do Smart Factory technologies cause at the operations level? How do you deal with such disruption?
It is important to keep in mind that digitization and any modern technology will certainly be disruptive. In such a scenario, companies need to ensure that the golden triangle of change is ready to make the transition i.e. people (who are at the crux), processes (which require human intervention) and technologies (that help perform processes).
Noting that the disruption will be positive, it is importance to acknowledge the positive effects that technology upgradation will bring to the efficiency of the manufacturing process. With AI and VR, there is scope for lesser errors, greater accountability and faster turn-arounds that help in addressing customer requirements in an agile manner.
For e.g: Recently when a customer in US had an issue and their service engineers were challenged, our R&D experts were able to simulate the scenario in our labs and offer a resolution. Thanks to the advancement of 3D technology, down-time, travel time, costs and efficiency could be managed remotely from halfway across the globe.
Technology upgradation calls for new skills set. How to deal with the challenge of skill upgradation?
Currently, the Indian manufacturing sector has the potential to grow six-fold by 2025 up to $1 trillion, creating up to 90 million jobs. With the current Government's Make in India initiative, this sector is set to grow further. The fact that India is a developing country gives us an added advantage that we are at the ‘start' line. This gives us the opportunity to apply knowledge that has been proved successful in similar societies and learn from their mistakes.
At Danfoss, we believe that the industry needs to engage more with universities to build a strong ecosystem for innovation and to enhance skill-sets of the future generation of decision makers. With the government's initiatives alongside the NSDC, we are confident of building a strong ecosystem for the future workforce of the country.
To foster the engineers of tomorrow, Danfoss has a comprehensive university engagement program that connects with student community in campuses across India. A unique partnership between industry and academia, the Danfoss university engagement initiative plays a key role in imparting industry-specific knowledge and the latest technology in climate and energy to engineering students, besides encouraging them to think innovatively.
While focus remains on building the skill-set of newer members of the workforce, it is also essential for the companies to invest in the periodic upskilling of their existing workforce in order to ensure continued efficiency that will translate to maximised productivity.
END