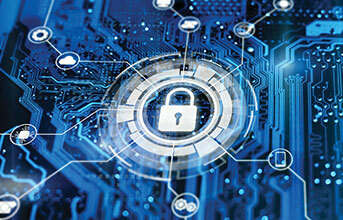
In a world where technological advancements dictate the pace of progress, the manufacturing sector is undergoing a revolutionary transformation. Digital manufacturing, characterised by the integration of advanced technologies such as artificial intelligence (AI), the Internet of Things (IoT), robotics, and additive manufacturing, is reshaping the landscape of production processes.
This shift promises unprecedented improvements in operational efficiency, product quality, and cost-effectiveness. However, with these advancements comes an increased vulnerability to cyber threats, necessitating robust cybersecurity measures to protect the digital infrastructure. This article delves into the digital manufacturing revolution, the challenges of transitioning, the critical need for cybersecurity, and the future trends shaping the industry.
The digital manufacturing revolution
Digital manufacturing is no longer a futuristic concept but a present reality that is transforming traditional production methods. By leveraging advanced technologies, manufacturers can achieve a level of efficiency and precision that was previously unattainable. AI-driven analytics allow for real-time decision-making, predictive maintenance, and optimised resource allocation, while IoT devices enable seamless communication between machinery, creating a highly interconnected and responsive manufacturing environment.
This transformation is driven by the need to remain competitive in a global market where customer demands are constantly evolving. The ability to produce high-quality products quickly and cost-effectively is a significant advantage that digital manufacturing provides. For instance, AI algorithms can analyse vast amounts of data to predict equipment failures before they occur, reducing downtime and maintenance costs. Similarly, IoT sensors can monitor the performance of machinery in real-time, allowing for immediate adjustments to ensure optimal operation.
Arvind Khanna, Director of Interiors Inc., highlights the tangible benefits of this transformation. "Production time for a batch of Wooden Planners has decreased by 35%, while the quality of each unit has seen a marked improvement. The reduction in material waste and labor costs has led to an overall decrease in production expenses by 18%."
The impact of digital manufacturing extends beyond traditional sectors. Subin Mitra, Co-founder & CEO, Groyyo, offers a compelling case study. "We developed technology that helps to gather shop floor data in vernacular languages, empowering our labor force to adopt and utilise digital tools effectively." Groyyo's partnership with Rue Fashion Private Limited exemplifies this impact. In just three years, the company tripled its production units, increased the number of machines from 40 to 400, and reduced rejections from buyers for quality reasons by over 50%. This showcases the significant improvement in product quality and reliability due to digital integration.
Overcoming transition challenges:
Transitioning from traditional manufacturing to a digital-first approach is fraught with challenges. Companies must navigate technological, organisational, and cultural hurdles to ensure a smooth implementation. One major obstacle is the integration of new technologies with existing, often outdated, machinery. This requires innovative solutions to ensure compatibility and seamless operation across the production line.
Technological integration involves retrofitting old machinery with new sensors and controllers or replacing them entirely with modern, digitally enabled equipment. This can be a costly and time-consuming process, but it is essential for achieving the benefits of digital manufacturing. Companies often face significant upfront costs for hardware, software, and training, but the long-term gains in efficiency and productivity make the investment worthwhile.
Rohit Saboo, President & CEO, National Engineering Industries Ltd., reflects on these challenges: "Our transition to a digitally driven factory, powered by Industry 4.0 technologies and the Industrial Internet of Things (IIoT), presented a very significant cultural and technological shift."
Cultural resistance is another significant barrier. Workers accustomed to conventional methods may be hesitant to embrace digital tools, fearing job displacement or struggling with new skill requirements. Overcoming this resistance involves comprehensive training programs and demonstrating the tangible benefits of digital manufacturing to the workforce. Clear communication and involvement of employees in the transition process can also help alleviate fears and build acceptance.
Mr. Manoj Kochar, President, ASPA, adds, "Navigating the integration of digital tools with existing processes requires a delicate balance between upgrading technology and managing the cultural shift within the organisation."
Cybersecurity in digital manufacturing
As manufacturing environments become more digitised, the threat of cyberattacks grows exponentially. Ensuring the security and integrity of digital manufacturing infrastructure is paramount to protect against data breaches, intellectual property theft, and operational disruptions.
Nathan Wenzler, Chief Security Strategist, Tenable, emphasises the critical need for comprehensive security solutions, "Manufacturers need preventive security solutions that offer total visibility of both IT and OT devices in the environment including broad asset inventory information as well as current configurations and security posture."
Cybersecurity in digital manufacturing requires a multifaceted approach. Preventive security solutions must offer comprehensive visibility of both IT and OT (Operational Technology) devices, including broad real-time monitoring of security postures. Intrusiondetection capabilities provide early warnings of potential threats, while continuous assessment protocols ensure that any changes in device configurations are promptly identified and addressed.
Aricson Pereira adds, "Given the critical nature of our work in medical device manufacturing, cybersecurity is a paramount concern. We've implemented advanced firewalls, intrusion detection systems, and rigorous training to protect our digital infrastructure."
The importance of cybersecurity cannot be overstated. A successful cyberattack on a manufacturing facility can have devastating consequences, including production halts, financial losses, and damage to the company's reputation. Advanced cybersecurity measures involve not only technological solutions but also human factors, such as employee training and awareness programs. Regular security audits and updates to systems and protocols are necessary to keep up with evolving threats.
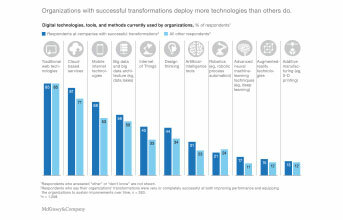
Sustainability through digital manufacturing
Digital manufacturing technologies also play a crucial role in advancing sustainability initiatives. By minimising waste, reducing energy consumption, and promoting sustainable practices, these technologies help manufacturers align with environmental goals while improving operational efficiency.
Sustainability in digital manufacturing is achieved through various means. AI-driven analytics optimise resource use, reducing material waste and energy consumption. IoT devices monitor and manage energy usage in real-time, ensuring that machinery operates at peak efficiency. Additionally, additive manufacturing techniques, such as 3D printing, enable the production of complex parts with minimal waste compared to traditional subtractive methods.
Subin Mitra highlights, "We've integrated ESG practices into all our factories. This includes ensuring good working conditions and continuous skilling of our workforce, which not only aligns with our sustainability goals but also enhances our global competitiveness."
For example, AI can analyse production processes to identify inefficiencies and suggest improvements. IoT sensors can track energy usage and environmental conditions, enabling precise control over machinery and reducing unnecessary consumption. Additive manufacturing allows for the creation of complex geometries with minimal material waste, making it a more sustainable option for producing certain parts.
Gaurav Bhagat, Managing Director, Consortium Gifts, notes, "Our adoption of digital manufacturing technologies has significantly reduced material waste and energy consumption, helping us achieve our sustainability targets while improving overall efficiency."
Meeting evolving customer demands
Digital manufacturing technologies enable companies to meet evolving customer demands for customisation, faster delivery times, and higher quality products. NEI's transition from traditional methods to real-time data access has revolutionised their operations. They can now quickly adjust production processes to meet specific customer requirements, streamline workflows to reduce lead times, and ensure that products meet the highest quality standards.
Arvind Khanna remarks, "Our ability to adapt quickly to customer demands has been greatly enhanced by digital manufacturing. It allows us to customise products more efficiently and meet tight delivery deadlines." Further Suhas Tejaskanda, Founder & CEO, Flying Wedge Defence & Aerospace, adds, "Robotic systems and real-time data access have enabled us to meet the precise needs of our clients in the aerospace sector, improving both product quality and delivery performance."
Visiting customers have praised NEI's digital initiatives, with some even collaborating to co-develop solutions. This collaboration has strengthened customer loyalty and satisfaction, demonstrating the direct impact of digital manufacturing on customer relationships.
Preparing for the future:
The future of digital manufacturing is poised to be reshaped by emerging trends such as Industry 4.0, Industry 5.0, robotics, cobots (collaborative robots), blockchain, and advanced data analytics. These trends will drive further advancements in efficiency, precision, and customisation of manufacturing processes.
Rohit Saboo emphasises, "Digital fluency will become non-negotiable, a basic requirement for participation in this evolving landscape. Staying ahead of emerging technologies will be crucial for maintaining a competitive edge."
Robotics and cobots are becoming increasingly prevalent in manufacturing environments. Cobots, designed to work alongside human workers, are particularly valuable in tasks that require a combination of precision and adaptability. These robots can handle repetitive and physically demanding tasks, allowing human workers to focus on more complex and valueadded activities.
Aricson Pereira looks ahead, "The future of digital manufacturing will be shaped by the integration of emerging technologies such as AI and augmented reality. These advancements will enhance our capabilities and revolutionise how we approach manufacturing."
Blockchain technology offers promising applications in supply chain management, providing secure, transparent, and tamper-proof records of transactions. This can enhance traceability, reduce fraud, and streamline logistics. By using blockchain, manufacturers can ensure the authenticity of their products and the integrity of their supply chains.
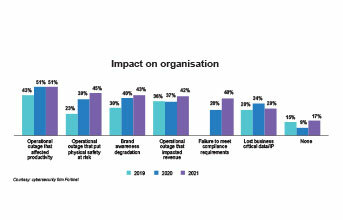
Collaborative innovation
Collaboration with industry players, technology providers, and academic institutions is essential for advancing digital manufacturing capabilities. By pooling resources and expertise, stakeholders can drive innovation, overcome challenges, and accelerate the adoption of new technologies.
Manoj Kochar underscores the importance of collaboration stating, "In this age of digitalisation, collaboration with ecosystem partners is crucial for success. It allows us to leverage each other's strengths and drive innovation collectively."
Suhas Tejaskanda adds, "We have formed strategic alliances with technology providers and academic institutions to advance our aerospace projects. This collaborative approach has been vital for staying ahead in a rapidly evolving industry."
Academic institutions play a crucial role in this collaborative ecosystem by conducting research and developing new technologies. Partnerships between academia and industry facilitate the transfer of knowledge and the commercialisation of innovative solutions. Additionally, these collaborations provide opportunities for training and upskilling the workforce, ensuring that employees are equipped with the necessary skills to operate and maintain advanced manufacturing systems.
The human element in digital manufacturing
While technology plays a central role in digital manufacturing, the human element remains crucial. Skilled workers are needed to operate and maintain advanced machinery, analyse data, and make informed decisions. As manufacturing processes become more digitised, the demand for workers with technical expertise and digital fluency increases. Subin Mitra highlights, "The human element is indispensable in digital manufacturing. Skilled workers who can harness the power of advanced technologies are key to driving innovation and maintaining competitiveness.
Investing in employee training and development is essential for ensuring that the workforce can effectively utilise digital tools and technologies. Companies must provide opportunities for continuous learning and skill development to keep pace with technological advancements. This not only enhances the capabilities of the workforce but also improves job satisfaction and retention. Gaurav Bhagat adds, "Our success in digital manufacturing is a testament to the importance of investing in our workforce. Continuous training ensures that our employees are equipped to handle new technologies and drive our business forward."
The role of government and policy
Government policies and regulations play a significant role in shaping the digital manufacturing landscape. Supportive policies can encourage the adoption of advanced technologies, promote innovation, and ensure the security and sustainability of manufacturing operations. Conversely, restrictive regulations can hinder progress and limit the potential benefits of digital manufacturing. Nathan Wenzler emphasises, "Government support and clear regulatory frameworks are critical for fostering innovation and ensuring the security of digital manufacturing operations." Rohit Saboo adds, "Clear and supportive government policies are vital for creating an environment where digital manufacturing can thrive. They help reduce barriers to adoption and encourage investment in new technologies.
Governments can support digital manufacturing through various means, such as providing funding for research and development, offering tax incentives for technology adoption, and establishing cybersecurity standards and guidelines. Collaboration between government, industry, and academia is also essential for developing and implementing effective policies.
Conclusion
The integration of digital manufacturing technologies is transforming the manufacturing industry, driving significant improvements in operational efficiency, product quality, and production costs. However, this transformation comes with increased cyber threats that require robust cybersecurity measures. Companies are at the forefront of this digital revolution, leveraging advanced technologies and collaborative efforts to secure their digital infrastructure and drive sustainability. As the industry continues to evolve, staying ahead of emerging trends and fostering innovation through collaboration will be key to maintaining a competitive edge.
The journey towards digital manufacturing is ongoing, with new technologies and trends continually reshaping the landscape. By embracing innovation, investing in cybersecurity, and fostering collaboration, manufacturers can navigate the challenges and seize the opportunities presented by the digital revolution. The future of manufacturing is digital, and those who adapt and innovate will lead the way in this transformative era.