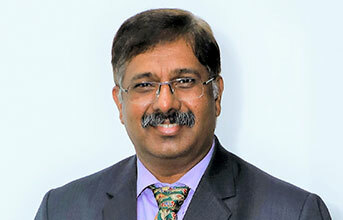
The age of smart manufacturing has long begun, driven by a strategic imperative to remain competitive and improve agility in response to rapidly evolving market dynamics. Manufacturers in India have embarked on their digital journey to transform their factory floors and supply chains with new-age technologies. Today, over 57 per cent of Indian companies make use of smart manufacturing – at the heart of which lies data.
DATA: THE PULSE OF SMART MANUFACTURING
The availability of high-quality, real-time data has made it optimal for manufacturers to gain smart insights, supporting better decision-making and improved efficiency. Data helps manufacturers reduce energy consumption, optimise supply chains, predict future outcomes for the business, and automate processes, which lowers costs and saves time. When applied intelligently, data also enhances product quality, increases productivity, detects production flaws, minimises downtime and instances of unanticipated maintenance.
However, despite having access to relevant data, most manufacturers still struggle to capture value from it. One reason for this gap is the challenge of ensuring interoperability between their information technology (IT) and operational technology (OT) infrastructure. The first question before the Indian industry is: with the integration of IT and OT and the convergence of these technologies, how do they ensure greater interoperability? Such integration is essential for grasping data and converting it into valuable, actionable insights.
MASTERING DATA FOR ACTIONABLE INSIGHTS
Ensuring connectivity between new and legacy machines is key, given that many legacy systems are built with modern architectures and open interfaces that enable easy connection. This ensures that all data can be captured even from the most fragmented systems in a scalable and secure manner. At the same time, it's essential to ensure that data is made available not only at the executive level but across the entire factory floor, supply chains, and between factories - horizontally and vertically. This approach enables real time knowledge and troubleshooting, nurturing the culture of a data-driven organisation.
Manufacturers are acutely aware that the transformational journey ahead presents challenges, such as:
• Digital Skills Drought
Without context, any data generated remains unused and useless. Applying context to data requires a workforce trained to understand and interpret the data devices in a value-added manner, enabling swift problem-solving based on facts and evidence. This means digital skills are necessary, whether through upskilling or reskilling by employers, around skills like data entry, automation, and analytics to create a functional and unified factory unit, and a consistent pipeline of digitally trained workers.
• Cultural Resistance
Cultural resistance can be a barrier when there is a lack of understanding of the organisation's transformation goals and worries about job security. This results in workers feeling less motivated by the company's cultural shift and the uptake of technology. The workforce will be the greatest asset in unleashing the power of data, deriving strategic and operational insights, and sharing data that supports the optimal functioning of a factory.
• Siloed Data Sources and Manual Processes
When data sources are isolated or siloed, it can impede the extraction of data from fragmented systems. Additionally, the use of paper-based processes by manufacturers leads to a lack of transparency or visibility, inaccuracies or errors, and data islands, making data less accessible and retrievable.
GETTING DOWN TO BRASS TACKS
Hope prevails in the face of challenges, and where there is a will, there is always a way. To make a manufacturing facility and its value chain data-driven, manufacturers must first run a digital transformation maturity assessment on data maturity. Performing an analytics evaluation assessment identifies the location of data assets and how they are being used. This process pinpoints gaps in manufacturing processes and singles out data-driven processes to be prioritised.
As successful data analysis depends on high-quality data, a manufacturer should define how data will be used and analysed to get the most accurate, actionable, and timely results. Firms must understand their OT and IT architectures and how to integrate them to harvest high-quality data. Building a cross-functional OT and IT team that shares data and analytics can create organisational-wide data security policies, fostering high-performing collaboration and a streamlined structure to achieve the best possible outcomes.
Organisations are recommended to take an iterative approach to data governance. This involves developing a policy that defines how data is processed organisation-wide, ensuring consistent and compliant data collection and storage, and establishing a solid data foundation from the start. To ensure success at this stage, manufacturers should work with an experienced partner.
A digital data-driven factory relies on workers skilled in digital tools. Here, an experienced partner can further help manufacturers bring their workforce up to speed with the latest digital tools. Gradually, the skills transfer should occur so that employees become familiar with using technology to solve problems, remaining competitive in today's revolutionary digital landscape.
Finally, manufacturers can adopt a unified namespace approach for a central data hub to ensure consistent data exchange across the organisation. Such contextualised and structured data allows machinery parts to be dissected and assessed, while enabling new analytics applications to be deployed at a faster rate.
CONCLUSION
The promise of data in transforming manufacturing is enormous. By working with a trusted partner who can help foster a data driven culture and identify the best business cases to drive a successful data-driven strategy, manufacturers can gain a competitive edge through operational insights, be more resilient to market disruption, and ensure that their growing volume of data brings about tangible business impact.