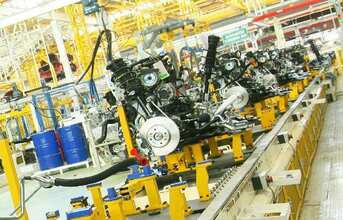
Manufacturers today understand the importance of an innovative, flexible and skilled workforce that is enabled by technology to make fast and efficient decisions and that can recognise and take advantage of new opportunities.
While the goal of technology in the manufacturing environment is uniting the shopfloor and the top floor for improved operational visibility, decision making and performance, the manufacturing environment has to date been a house divided.
Traditionally, operational visibility in the realm of the shopfloor has been provided by Manufacturing Execution Systems (MES) supporting real-time process control scenarios and quality initiatives, whereas Enterprise Resource Planning (ERP) has been in use upstream in the manufacturing operations, primarily supporting optimised scheduling and planning.
Each system on its own can provides myriad benefits. But today's manufacturers aren't willing to settle; instead, desiring to drive improved performance and competitive advantage they are integrating these two systems and these two worlds to leverage the best of both.
Evaluating ERP
ERP is no longer simply about cutting costs, but rather about enabling businesses to grow and take advantage of new opportunities and avoid unexpected risks. Companies now need the next evolution of ERP systems that can support collaboration, adapt to unique and dynamic environments, enable improved customer satisfaction and new business, and which can drive growth as well as control costs.
ERP system architectures that empower employees by uniting social, mobile, and analytic capabilities can help support innovation. Employees can then raise the individual and collective performance within the company by leveraging real-time shared access to the same repository using a set of tools that meets the specific needs and requirements of each user.
(Continued on the next page)