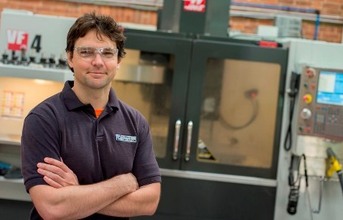
If you're going to change the way things are made, you need very good ideas and pertinacious investors. When Ben Halford founded Surface Generation in 2000 as a spin-off from an engineering consultancy business, he had both. Which is just as well because a few years into its business plan, Surface Generation's future hung in the balance.
"The financial crisis of 2007/8 hit us hard," says Halford. "But, with the support of our shareholders we got our heads down and developed something in which we'd seen a nascent interest: a rapid heating and cooling technology for composites parts production. And that's what we have today."
The technology found a market immediately and the company's operations grew dramatically. "We now have 30 people employed here and we are working hard to keep up with demand from some very well known firms around the world."
Surface Generation claims its patented Production to Functional Specification (PtFS) technology provides manufacturers in the aerospace, automotive and consumer electronics sectors with a significant improvement in cost, quality and delivery for precision moulded parts.
"Most composite parts are ‘cooked' - heat cured, in an autoclave," says Halford. "But that's an isothermal process, where the temperature the part is exposed to is constant. If you want to make parts of varying sectional thickness, perhaps using a combination of different materials, it can't be done in an autoclave, as different areas of the part need to be heated to different temperatures and cooled at different rates."
(Continued on the next page)