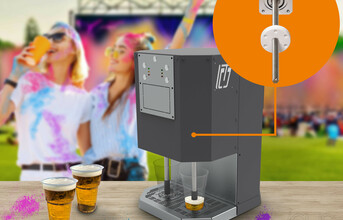
One Two Beer GmbH has introduced an automatic beer tap. This state-of-the-art device features a mobile tap head that can swiftly and precisely fill beer cups in just five seconds, eliminating the age-old issue of foam overflow.
The idea is the integration of igus drylin linear guide technology, characterised by hygienic standards, lubrication-free operation, and durability.
Automatic Beer Tap System
The One Two Beer automatic beer tap system is engineered to cater to large crowds efficiently. The system consists of two plastic cups placed side by side, resembling the setup of a coffee machine. With a simple press of a button, the dispensing heads facilitate a flawless beer pour.
This bottom-up filling approach eliminates the problem of foam overflow, allowing beer enthusiasts to enjoy their beverages without any delay.
Engineering Challenges
Developing the automatic beer tap posed a unique set of technical challenges, as said by Tamás Kozma, Chief Information Officer at One Two Beer GmbH. Kozma, "To achieve rapid beer dispensing, a high-speed linear guide with minimal friction was essential." Furthermore, the system needed to maintain a precision level of up to one-tenth of a millimetre.
Hygienic and Lubrication-Free Linear Guide
The linchpin of the system's efficiency lies in the operation of the linear guide. The tap is affixed to a flange lead screw nut sourced from the igus dryspin JFRM series.
The lead screw nut is constructed from FDA-compliant high-performance plastic, an inherently self-lubricating material that ensures smooth and low-friction dry operation. Moreover, this polymer nut resists the accumulation of dirt, simplifying the cleaning process with water or high-pressure methods.
Enhanced Efficiency
Furthermore, the design of the lead screw incorporates enlarged thread flanks, which increase the surface area for power transmission.
This asymmetrical thread design extends the service life by approximately 30 per cent compared to symmetrical trapezoidal threads. Additionally, the flattening of the flank angles of the lead screw nut and lead screw itself contributes to an efficiency rate of 82 per cent, surpassing industry standards.