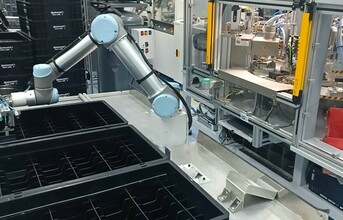
Technology company Continental is on the course to achieving 100 percent carbon neutrality along its entire value chain by 2050 at the latest. In this pursuit, Continental has been auditing and recognizing all its manufacturing plants across the globe on sustainability practices and awarding the Green Plant Label (GPL) certification. The Bangalore plant was recently audited and has achieved yet another milestone by receiving a gold certification in Green Plant Labeling. After the Regensburg plant in Germany, the Bangalore plant is the second location to receive a gold certification within Continental, from among 58 Automotive plants globally. The Green Plant Label evaluates criteria such as energy efficiency, water consumption, emission control, waste and recycling management, and innovations in the research and development (R&D) space.
According to Phanindra Karody, Head of the Bangalore Plant, Continental Automotive India, "The gold certification in Green Plant Label is a remarkable feat for the Bangalore plant and we were steadfast in our efforts to achieve this. For us, sustainability is at the core of our business and manufacturing practices. At our state-of-the-art plant, we follow Industry 4.0 practices in all areas enabling smart manufacturing and data-driven operational management. The Bangalore plant is a fine example and a step in the right direction in realizing Continental's vision to achieve carbon neutrality."
"GPL is an internal certification with tough targets and it is an outstanding achievement for our Bangalore plant to reach the Gold level. We congratulate the whole team for being one of the first plants to reach this high standard. Through our various processes and actions, we aim to speed up our course to achieve carbon neutrality at the earliest possible." said Dirk Remde, Head of Automotive Sustainability.
Continental has identified four focus areas for achieving its sustainability goals—carbon neutrality along Continental's entire value chain, emission-free mobility and industry, a circular economy, and a responsible value chain. Continental aims to fulfill its ambition by 2050 at the latest.
Continental is working towards making all of its production processes carbon-neutral by 2040 by meeting the targets of the global Paris Climate Agreement, which aims to keep the rise in global temperatures well below 2°C, and ideally below 1.5°C. The organization is doing so by reimagining the entire global value chain of its products, from the procurement of materials, through manufacturing, transport, and consumption, to recycling at the end of use. Continental is working intensely on reducing its CO2 footprint by purchasing green electricity for all plants worldwide since 2020.
Further, with the circular economy being the economic model of the future, Continental is working towards creating a responsible value chain where each stakeholder including suppliers, and customers creates ecological, economic, and social value for society. Working with responsible suppliers and vendors and leveraging automation, Continental has set the target of increasing its waste recycling rate to 95 percent by 2030.
Industry 4.0 Practices
In the quest of establishing a sustainable manufacturing ecosystem, Continental has adopted digitization and automation of various processes. The Bangalore plant is the largest electronics manufacturing plant of Continental in India and is symbolic of a smart factory. Technologies such as collaborative robots (Cobots), Augmented Reality (AR), Artificial Intelligence (AI) for face recognition, automated replenishment systems, automated optical inspection, automated guided vehicles (AGV), and Big Data applications are implemented on the shop floor, help in operational efficiency, meeting quality standards, stay consistent in precision, and maintain a high level of transparency.