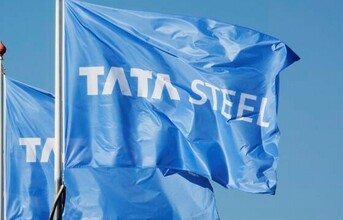
Tata Steel has almost halved energy costs at its steel facility in Düsseldorf after building an innovative new power plant.
The combined and heat power (CHP) plant will reduce the site's annual energy costs by about €1 million (£750,000) and cut emissions of CO2 by almost 50%. The power station is the company's first of its type and has been built on the premises of Hille & Müller, part of Tata Steel's plating business.
The enterprise, which employs 275 people, is one of Europe's leading producers of specialised steel which is used to case household and car batteries. It was also the first company in the world to produce electroplated steel strip.
As well as producing electricity, Tata Steel's €2.8 million (£2.1m) gas-fuelled CHP plant turns by-product heat into steam, which is used in manufacturing processes as well as to heat buildings for employees. The new plant will reduce CO2 from the site by the equivalent emissions of about 2,000 homes.
Friedmar Schittko, MD, Hille & Müller in Düsseldorf, explained: "By installing this new plant we have taken a decisive step towards our long-term aim of becoming self-sufficient in energy, which improves our competitiveness and makes our operations more resource-friendly.
"In future we will be able to produce about half of our own electricity in Düsseldorf - about 13 megawatts hours per year. This is equivalent to supplying almost 3,000 households with electricity.
"We are also looking into whether we can supply heat to neighbouring businesses."
Following a testing phase, the CHP plant is now fully operational. The plant consists of two high-temperature boilers and a power-heat cogeneration facility. The 2,500bhp engine (equivalent to about 25 car engines) for the power-heat cogeneration runs on natural gas and produces approximately 2,000 kW of electricity. The plant also produces about 2,000 kW of by-product heat, which is turned into steam and used in manufacturing processes and to heat buildings for employees.
The installation of the CHP plant is just one component of Tata Steel's strategy to improve its own energy management. Hille & Müller has also implemented an energy management system according to the ISO 50001 standard, certified by the technical control board (TÜV).
END