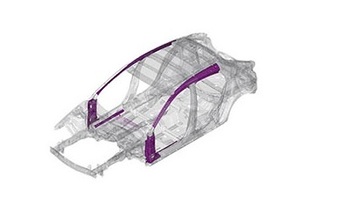
Mazda Motor Corporation, working separately with Nippon Steel & Sumitomo Metal Corporation and JFE Steel Corporation, has developed the world's first cold-stamped vehicle body parts made from 1,310 MPa-class high-strength steel. The parts are used in Mazda's new-generation Skyactiv-Vehicle Architecture, which will underpin upcoming models starting from the all-new Mazda.
High-strength steel enables automakers to make parts from thinner sheet metal while retaining the necessary yield strength. This results in a lighter vehicle body, which contributes to improved handling stability and fuel economy. A strong body is also essential to ensure crash safety performance, and the application of higher-strength steel has been widely anticipated.
Until now, cold-stamping of vehicle body structural members has only been possible with 1,180 MPa or lower-classed steel, due to the material's formability and the difficulty of ensuring dimensional accuracy after processing. Working in collaboration with the above-mentioned companies, however, Mazda has found an appropriate set of processing conditions that make the process possible with 1,310 MPa-class high-strength steel.
The all-new Mazda uses 1,310 MPa-class high-strength steel for the front pillar inner, the roof rail inner, the hinge pillar reinforcement, the roof rail reinforcement, the No. 2 crossmember and the side sill inner reinforcement, saving about 3 kilograms over the same parts in the previous model.