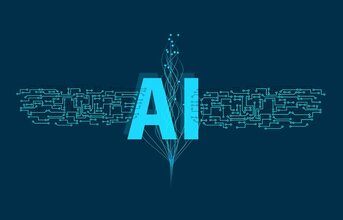
Zebra Technologies Corporation, a leading digital solution provider, enabling businesses to intelligently connect data, assets, and people, has announced the findings of its 2024 Manufacturing Vision Study. The study showed that globally, 61 per cent of manufacturers expect AI to drive growth by 2029, up from 41 per cent in 2024. In APAC, including India, 68 per cent of manufacturers expect AI to drive growth by 2029, increasing from 46 per cent in 2024. This surge in AI adoption, combined with 92 per cent global and 87 per cent of APAC survey respondents prioritising digital transformation, underscores manufacturers' intent to improve data management and leverage new technologies that enhance visibility and quality throughout the manufacturing process.
While digital transformation is a priority for manufacturers, around 30 per cent to 40 per cent of global and APAC, including India, recognise achieving it is fraught with obstacles, including the cost and availability of labour, scaling technology solutions, and the convergence of information technology and operational technology (IT/OT).
Visibility is the first step to transformation—through adopting AI and other new technologies. This enables manufacturers to leverage data more effectively to identify, react to, and prioritise problems and projects to deliver incremental efficiencies across the manufacturing process, ensuring the greatest impact upfront.
"Manufacturers struggle with using their data effectively so they recognise they must adopt AI and other digital technology solutions to create an agile, efficient manufacturing environment", said Subramaniam Thiruppathi, Director of Sales for India and Sub-Continent, Zebra Technologies. "As India and APAC manufacturers gear up for AI-driven growth, our focus on leveraging advanced technologies and optimising data utilisation will be pivotal. With India's manufacturing sector set to hit US$ 1 trillion by 2025–26, our latest innovations, including the FXR90 ultra-rugged fixed RFID readers and ZS300 electronic sensors, will empower ecosystem players to significantly enhance operational efficiency and data-driven decision-making".
Focusing on Closing Visibility Gaps
Although manufacturers say digital transformation is a strategic priority, achieving a fully connected factory remains elusive. Visibility is key to optimising efficiency, productivity, and quality on the plant floor, yet a large visibility gap exists. Only 16 per cent of manufacturing leaders globally report having real-time, work-in-progress (WIP) monitoring across the entire manufacturing process, while this is true for more of APAC manufacturing leaders, at 25 per cent.
While nearly six in 10 (57 per cent globally, 63 per cent in APAC, including India) manufacturing leaders expect to increase visibility across production and throughout the supply chain by 2029, around one-third of leaders (33 per cent globally, 38 per cent in APAC, including India) say getting IT and OT to agree on where to invest is a key barrier to digital transformation. Adding to these obstacles, 86 per cent of global manufacturing leaders agree they are struggling to keep up with the pace of technological innovation and to securely integrate devices, sensors, and technologies throughout their facilities and supply chain, with 82 per cent of APAC manufacturing leaders in agreement.
Augmenting the Workforce, Elevating Value and Efficiency
Zebra's study found manufacturers are shifting their growth strategies by integrating and augmenting workers with AI and other technologies to transform manufacturing and build a skilled workforce over the next five years. Nearly three-quarters (73 per cent) of global manufacturing leaders plan to reskill labour to enhance data and technology usage skills, as seven in 10 expect to augment workers with mobility-enabling technology. These sentiments were shared by 76 per cent and 75 per cent of APAC manufacturing leaders respectively.
The technology tools being implemented by manufacturing leaders include tablets (51 per cent globally, 52 per cent in APAC, including India), mobile computers (55 per cent globally, 53 per cent in APAC, including India), and workforce management software (56 per cent globally, 62 per cent in APAC, including India). In addition, six in 10 of manufacturing leaders (61 per cent globally, 65 per cent in APAC, including India) plan to leverage wearable mobile computers to augment their evolving workforce.
Manufacturing leaders across the C-Suite, Information Technology (IT), and Operational Technology (OT) understand how labour initiatives must extend beyond improving worker efficiency and productivity with technology. Six in 10 global and APAC leaders rank ongoing development, retraining/upskilling, and career path development to attract future talent as a high priority for their organisations.
Advancing Automation to Optimise Quality
Overall, the quest for quality has intensified as manufacturers across segments must do more with fewer resources. According to the survey, manufacturing leaders say today's most significant quality management issues are real-time visibility (33 per cent globally, 40 per cent in APAC, including India), keeping up with new standards and regulations (29 per cent globally, 30 per cent in APAC, including India), integrating data (27 per cent globally, 31 per cent in APAC, including India), and maintaining traceability (27 per cent globally and in APAC, including India).
Manufacturing leaders' technology implementation plans will address these challenges. Over the next five years, many plan to implement robotics (65 per cent globally, 72 per cent in APAC, including India), machine vision (66 per cent globally and in APAC), radio frequency identification (RFID) (66 per cent globally, 72 per cent, factors including the need to provide the workforce with high-value tasks (70 per cent globally, 75 per cent in APAC, including India), achieve service level agreements (69 per cent globally, 70 per cent in APAC), and add more flexibility to the plant floor (64 per cent globally, 66 per cent in APAC, including India).